가스 경보기 이론
1. 시스템 개요
산업의 고도성장으로 인하여 많은 공장 및 연구소. 학교. 공공시설물등에서 폭발성 가스 및 유 독성 가스의 생산, 저장, 운송, 사용, 폐기 등으로 인한 푹발사고 및 안전사고로 산업재해가 빈 번히 발생되고 있다. 이러한 가스에 의한 위험성은 가연성가스에 의한 인화, 폭발, 독성가스에 의한 중독사고등, 산업재해의 위험으로부터 귀중한 생명을 보호하는데 목적을 두고있다
2.가스검지기의 종류 및 검지방법
2-1. 가스검지기의 검지방법
가스를 검지하여 그 농도를 전기신호로 변환하는 가스검지부는 가장 중요한 구성부 분이 고, 이부분의 역할이 검지기 성능을 결정한다. 가스검지 방법은 확산식과 흡입식의 2가지 방법이 있는데 모두 가스검출단부 근처에 설치된다.
2-2. 가스 검지기 구성
2-2-1. 종류
가스별 : 가연성, 독성, 산소 검지기
용도별 :
산업용 - 산업현장의 조건 : 온도, 습도, 변화, 풍향, 풍속, 날씨변화 등에도 안 정된 출력을 얻을수 있는 신뢰성이 높은 검지기
일반용 - 실내 등의 일정한 조건아래 사용 가능한 제품으로 산업용으로 사용하는 것은, 안정성에 문제가 있다.
감시 목적별 :
휴대용 - 작업자가 작업도중 휴대할수 있는 검지부로서 센서, 지시계, 경 보계등이 일체식으로 되어있다.
고정식(설치용) - 일정한 장소에 설치 고정되어 24hr/Day로 연속 감시하 는 감지기로 감지부와 지시부가 분리되어있다.
검지기 방식별 :
확산식 - 검지센서가 대기중에 노출되어 있어 측정가스의 확산에 의해 검출하는 방식
흡입식 - 측정 가스를 펌프나 AIR ASPIRATOR에 의해 강제 흡입하여 검지(확산식설치 불가능한 장소에 이용)
2-3. 확산식, 흡입식의 구조와 특징
2-3-1. 확산식
확산식 가스감지기는 가스가 누설되면 대기중의 공기와 혼합된 가스의 농도를 측정하는 방법으로서 일반적으로 가장 많이 적용되는 방법이다. 확산식 감지기는 누설시 기류등 의 받을수 있으므로 설치시 위치고려와 아울러 신속하게 감지할수 있는곳에 설치하여 가스누설을 측정하도록 한다.
2-3-2. 흡입식(산업용)
진동펌프 혹은 인젝타 등으로 구성된 통기부를 검지부와 합해서 설치하여 강제적으로 가스를 흡입해서 검지부에 가스를 접촉시키는 방식이다. 협소한장소, 근접하기 위험한장소, 기타 높은 장소나 낮은 장소와 같은 보수시에 안으로 들어 가기가 곤란한 장소에 사용된다. 이와같은 곳에 검지단부를 정한경우에 최대한 안으로 들어간 장소에 검지부를 설치하고 검지단부 까지를 가스채최관해서 결합한다. 가스의 흡입로에 가스검지를 방해하는 조건을 개선하기 위해 먼지, 습도, 온도조절 등의 전처리장치를 삽입하는 것도 가능하다. 인화, 폭발방지상, 전기기기의 설치가 제한되는 장소의 가스검지도 흡입식을 사용하는 것으로 가능하다.
3. 가스감지기의 가스별 분류
3-1. 가스감지기의 분류
- 가연성 가스 : 공기중에 산소와 반응하여 연소하는 가스 ( LNG, LPG, CH4, H2, i-C4H10, etc.. )
- 독성가스 : 인체 허용농도(TLV)가 200ppm 이하인 가스 ( NH3, CO, CL2, COCL2, VCM, etc.. )
- 불활성 가스 : 분자 구조가 안정되어 있어 화학 반응을 하지않는 가스 ( He, Ar, Ne, etc.. )
- 조연성 가스 : 연소하는 것을 도와 주는 가스 ( O2 )
- 불연성 가스 : 전혀 연소하지 않는 가스 ( N2, CO2, Freon, etc.. )
3-2. 비중에 따른 분류
- 중가스 : 공기보다 무거운 가스 ( i-C4H10, C2HOH, VCM, etc.. )
- 경가스 : 공기보다 가벼운 가스 ( H2, CH4, He, etc.. )
3-3. 가스종류별 검지농도
가스의 종류 | 검지 농도 |
가연성 가스 | 폭발하한계의 1/4 이하 |
독 성 가 스 | 허용농도치 이하 |
산 소 | 25% 이하 18% 이상 |
4. 용어설명
4-1. % LEL : LOWER EXPLOSIVE LIMIT ( 폭발 하한치 )
가 연성 가스가 공기중의 산소와 혼합되어 있는 경우, 혼합가스 조성에 따라 점화원 에 의해 착화된다. 즉 혼합가스의 연소 가능한 범위를 폭발 범위라 하며, 그 최저 농도를 폭발하한치(LEL), 최고농도를 폭발상한치(UEL)이라고 한다.
4-2. TLV : THRESHOLD LIMIT VALUE (허용농도)
- 유독 가스 등이 공기중에 존재하는 작업장에서 1일 8시간 정도 작업을 매일 계속하 여도 건강에 이상이 없는정도.
- ACGIH, 일본산업 위생학회에서 권고하는 농도임.
- 이 농도는 작업시간중의 시간 가중농도 평균치를 나타내므로 일시적으로 이 기준 농도보다 높은 농도에서 작업하는 것은 허용 될 수있다. 예). 암모니아 (NH3) : 25ppm 일산화 탄소 (CO) : 50ppm, 염소 (CL2) : 1ppm, 염화수소 (HCL) : 5ppm
4-3. STEL (Short Tern Exposure Limit )
- 작업자가 15분 이내에 작업할 때 허용될수 있는 농도
4-4. %, ppm, ppb
- 양을 나타내는 단위로서, 가스일 경우에는 부피비를 뜻한다.
- PERCENTAGE (%) : 백분율
- ppm : 백만분율 ( PART PER MOLLION )
- ppb : 10억분율 ( PART PER BILLION ) - 1% = 10,000ppm = 1,000,000,000ppb - 1ppm = 1,000ppb
4-5. LPG ( LIQUIFIED PETROLIUM GAS )
- 액화 석유가스로서 주성분은 프로판(C3H8 약 85%)이다.
- 공기보다 무겁다.
4-6. LNG ( LIQUIFIED NETURAL GAS )
- 액화 천연가스로서 주성분은 메탄(CH4)이다.
- 공기에 비해 가볍다.
가스누출 감지 검지 장치의 설치 기준
가스누출 감지 및 검지 장치의 설치 기준은 산업 안전과 화재 예방을 위해 매우 중요한 요소입니다. 일반적으로 다음과 같은 기준이 적용됩니다:
설치 장소
- 누출 위험이 높은 지역: 펌프, 압축기, 밸브 연결부 등 가스가 새어나올 가능성이 높은 곳.
- 밀폐된 공간: 가스가 축적될 가능성이 있는 실내 공간이나 환기가 어려운 장소.
- 저장 시설: 가스 저장 탱크 주변 및 대량 누출 위험이 있는 장소.
- 폭발 위험 구역: 인화성 가스가 존재하는 산업 시설 내 특정 구역.
설치 기준
- 감지기 배치: 가스의 특성에 따라 공기보다 가벼운 가스는 천장 부근에, 무거운 가스는 바닥 근처에 설치.
- 감지기 간격: 시설의 크기와 가스 확산 특성을 고려하여 적절한 간격으로 배치.
- 경보 시스템 연계: 감지기가 가스를 탐지하면 즉시 경보를 울리고 환기 시스템을 작동하도록 설정.
- 정기 점검 및 유지보수: 감지기의 정확한 작동을 위해 주기적인 검교정 실시.
관련 규정
- KS C 6591: 가연성 가스 감지기의 설치 및 유지보수 기준.
- 화학물질관리법: 유해 화학물질 취급 시설의 검지 및 경보 설비 설치 의무.
- KOSHA GUIDE P-166-2020: 산업 안전을 위한 가스 감지기 설치 지침.
송풍기
송풍기 설치, 운전 및 보수 요령서.
1. 본 설명서는 본 장치를 취급하는 기술자에게 정확한 운전, 보수 취급방법을 이해시키기 위한 것입니다. 따라서 취급자는 본 설명서를 숙독하여 완전히 이해한 후 본 장치를 취급 하시기 바랍니다.
2. 본 설명서는 운전 보수 상에 일어날 수 있는 문제점을 되도록 망라하였으나. 우발적인 문제 혹은 예측불허의 사고 등에 대해서는 수록되어 있지 않습니다.
따라서 문제점 혹은 불명확한 문제점이 있으면 폐사에 문의하여 주십시오.
3. 본 설명서에 규정되어 있는 제한치를 준수하여 무리한 취급을 피하고 정확한 점검으로 사고를 미연에 방지할 수 있도록 하여 주십시오
4. 본 설명서는 운전 및 보수 취급방법을 이해시키기 위한 것입니다. 따라서 취급자는 본 설명서를 숙독하여 완전히 이해한 후 본 장치를 취급하시기 바랍니다.
5. 운전불능, 고장 등의 사고가 발생한 경우에는 즉시 아래의 요령대로 연락하여 주시기 바 랍니다.
1) 사고가 발생한 부품명 및 부위
2) 이상상태의 내용과 사고 발생 전/후 상세내역
3) 연락처 : 경기도 시흥시 정왕동 879-610
전화 : T,031-498-8787 F,031-498-4287
6. 본 설명서에 기재된 사항은 폐사가 지금까지의 얻은 지식과 경험을 기준으로 하고 있어 설명서 발행시점에 있어서 가장 우수한 판단기준을 수록하였습니다.
운전준비, 운전조작, 점검, 보수, 안전 등에 대하여 본 취급설명서에 수록되어 있는점이 완 전하게 실행되지 않아 발생한 사항에 대하여 전적으로 본인의 책임임을 양지하여 주시기 바랍니다.
보다 중요한 것은 항상 안전작업을 취우선으로 생각하시고 쾌적한 작업환경, 희망찬 보람 의 터전이 되길 바랍니다.
목 차
1. 개 요 ................................................................................................. 3
2. 반 입 ................................................................................................. 3
2. 1 대 조 ........................................................................................... 3
2. 2 하 역 ........................................................................................... 3
2. 3 보 관 ........................................................................................... 3
2. 4 맞춤 마크 ........................................................................................ 3
2. 4. 1 CASING 맟춤 마크 ..................................................................... 4
2. 4. 2 CASING .................................................................................... 4
2. 4. 3 DAMPER ................................................................................... 4
2. 4. 4 BEARING HOUSING ................................................................... 4
3. 설 치 .................................................................................................. 5
3. 1 설치전 준비 ...................................................................................... 5
3. 1. 1 기초 치수의 확인 ....................................................................... 5
3. 1. 2 기초 조정 .................................................................................. 5
3. 2 현장 조립 및 설치 ............................................................................. 5
3. 2. 1 편지지형 .................................................................................... 6
3. 2. 2 양지지형 .................................................................................... 6
3. 2. 3 고온 송풍기의 설치 ..................................................................... 8
3. 2. 4 BEARING 조정 및 BEARING HOUSING의 위치 설정 ....................... 9
3. 2. 5 CASING의 조립과 조정 ............................................................... 10
3. 2. 6 기초 BOLT의 묻음과 재조정 ........................................................ 11
3. 3 DUCT 연결과 CASING INSULATION .................................................... 12
4. 운 전 .................................................................................................. 13
4. 1 시운전전 검사 ................................................................................... 13
4. 2 기동후의 점검 ................................................................................... 14
4. 3 운전중의 점검 ................................................................................... 15
4. 4 정 지 ............................................................................................ 16
5. 보 수 .................................................................................................. 17
5. 1 IMPELLER ........................................................................................ 17
5. 2 구름 BEARING ................................................................................ 17
5. 2. 1 BEARING HOUSING이 상하 분할형이 아닌 경우 .......................... 18
5. 2. 2 BEARING HOUSING이 상하 분할형인 경우 .................................. 19
5. 3 METAL BEARING ............................................................................. 20
5. 3. 1 분 해 .................................................................................... 20
5. 3. 2 틈새조정 .................................................................................. 20
5. 3. 3 조 립 .................................................................................... 21
5. 4 전동장치 .......................................................................................... 21
5. 5 윤활유 ............................................................................................. 22
5. 6 DAMPER .......................................................................................... 23
1. 개 요
송풍기의 종류는 형식, 용도, 사용조건 등에 의해 다양하게 구분되지만 그 주요부분은 Casing Impeller, shaft, Bearing, Coupling, (또는 V-Pulley), Bed 및 풍량제어장치 등으로 구성되어 있습니다.
납입된 송풍기의 성능, 형식, 구성부품, 재질, Bearing의 배치, 추천 윤활제에 대해서는 조립 외형도, (또는 단면도) 와 Data sheet를 참조하여 설치에 앞서 충분히 숙지해 두어야 합니다.
본 취급 설명서는 당사 송풍기 전반에 대한 설치 및 조립, 운전, 보수요령에 대하여 설명한 것으로서 납입된 송풍기의 효과적인 운용을 위해 활용해 주십시오.
2. 반 입
2.1 대 조
송풍기가 반입되면 납품서와 현품을 대조 확인해 주십시오.
각 송풍기의 명판에는 제작번호가 각인되어 있으므로 당사로의 조회 질문 등에는 이 번호를 사용해 주십시오.
2.2 하 역
(1) 축과 조립된 Impeller를 달아 올릴 때 로프를 잘못 걸시 축에 흠집을 주지 않도록 주의하여 주십시오. 특히 >Bearing부나 기타 부품이 조립된 부분에는 절대로 로프가 직접 닿아서는 안됩니다.
(2) Impeller를 지면에 내려놓을 때는 직접 지면에 놓지 말고 침목을 넣어 받쳐 주십시오.
(3)Casing을 매달 때는 로프에 걸리는 하중이 균일하도록 주의하여 주십시오.
2.3 보관
(1) 포장된 부품은 현품 대조 후 파손이나 발청을 막기 위해 될 수 있는 대로 포장을 풀지 마십시오.
(2) 회전 부품은 가능한 옥내에 보관하시고 부득이 옥외에 보관하는 경우에는 방우처리를 완전히 해주십시오.
(3) 전장품은 반드시 옥내에 보관하여 주십시오.
2.4 맞춤 마이크
대형 송풍기는 부품이 분할 발송되므로 조립시 맞춤 마크에 유의하여 주십시오. 단, 조립상태로 발송된 경우에는 맞춤 마크가 없으므로 분해시 (예;보수기간중) 주의를 요합니다.
2.4.1 CASING 맞춤 마이크
Casing이 분할 발송되는 경우 그 각각에 上, 下 혹은 No.1 No.2등의 표시가 되어있습니다. 그리고 흡입 BOX가 있는 경우 축관통부 부근에 전동기측인가 반전동기측인가를 나타내는 ‘M', 'F' 마크를 넣고 있습니다.
2. 4. 2 CASING 흡입구
흡입구의 수직위치를 구별하기 위해 흡입구 상부에 고리를 붙이거나 ‘上’의 표시를 하고 있습니다.
2. 4. 3 DAMPER
Damper Flange면의 일부가 착색되어 있으므로 이것과 같은 색의 Casing Flange에 Damper가 연결되어야 합니다.
2. 4. 4 BEARING HOUSING
Bearing Housing이 축에 미리 조립되어 있거나 혹은 Bed에 고정되어서 납품되는 경우에는 설치 위치가 쉽게 구별되지만 별도로 납품되어 혼동의 우려가 있을 때에는 그것이 전동기측인지 반전동기측인지를 나타내는 ‘M', 'F' 마크를 Bearing Housing과 Bearing Housing Bed에 표시하고 있습니다. Metal Bearing의 경우에는 Bearing 분할 면에도 ’M', 'F' 마크를 표시합니다.
3. 설치
3.1 설치 전 준비
3.1.1 기초 치수의 확인
기초치수, 기초Blot의 위치, 부품의 배치를 조립외형도와 대조 확인해 부십시오.
3.1.2 기초조정
(1) 통상 기초 Bolt 양쪽에 Backer Plate를 배치하고 설치하므로 기초 높이에는 이 여유가 고려되어야 합니다. 또한 모르타르 그라우팅 (Mortar Grouting)으로 고정 되기 전에 미리 Backer Plate의 Leveling을 봐 두어야 합니다.
(2) Backer Plate위에는 Taper Liner (1/10~1/15)또는 Shim Liner를 넣어서 설치시 조정을 계속하게 되는데 Leveling이 끝난 후 Backer Plate 와 라이너를 용접하여 두면 운전중 Fan 진동으로 발생될 수 있는 Centering Error를 방지할 수 있습니다. 형강위에 설치되는 경우에도 상기에 준하여 시행해 주십시오.
3.2 현장조립 및 설치
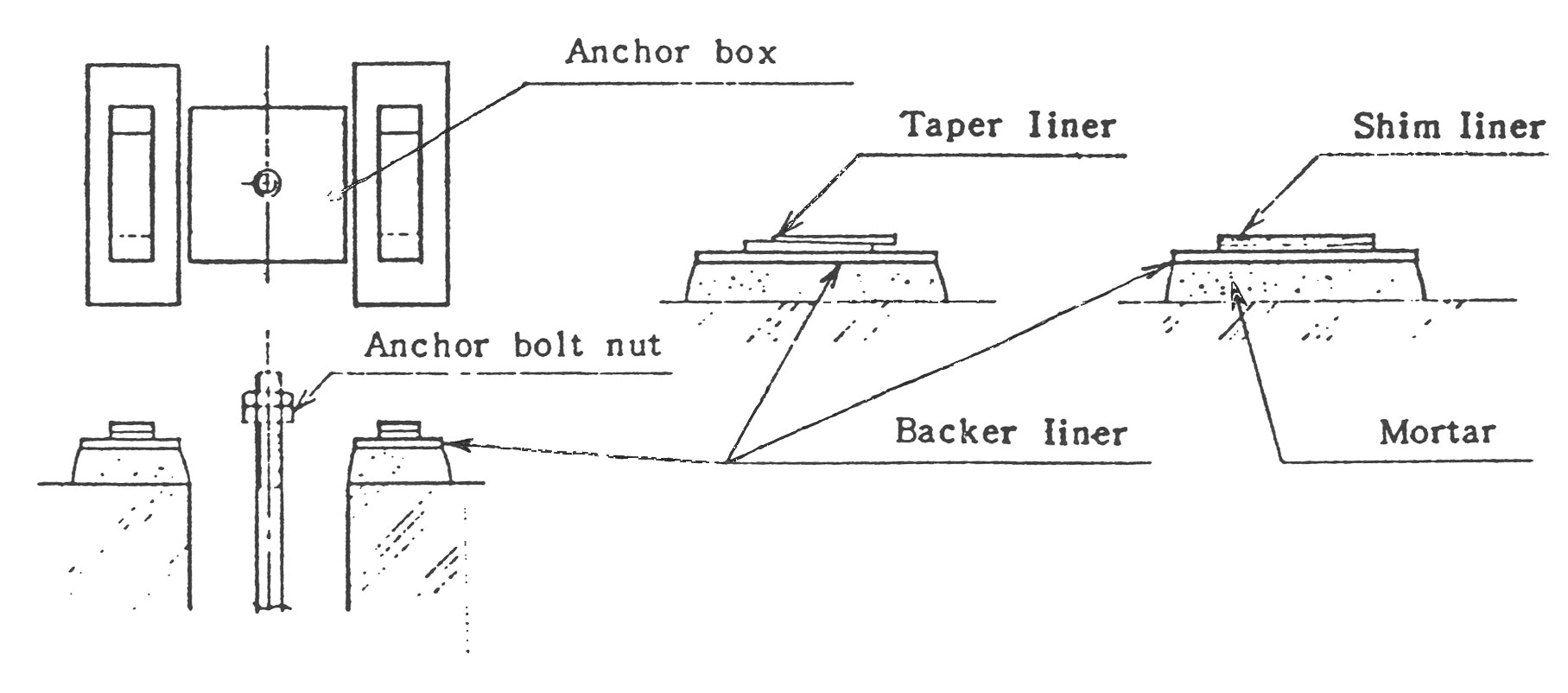
조립에 앞서 Casing 내부의 이물질을 제거하고, Bearing Housing 내부에도 이물질이 들어가지 않도록 하며, 필요시 백등유 등으로 깨끗이 씻어냅니다. 만약 Bearing에 이물질이 유입되면 중대한 사고의 원인이 됩니다.
3.2.1 편지지형 (Bearing이 Impeller 한쪽에 배치되어 있는 경우)
(1) CASING의 설치
Casing이 Bearing, Motor와 함께 공통 Bed위에 이미 조립도어 납품된 경우에는 그대로 기초위에 올려놓습니다. Casing이 분할되어 있을 때는 먼저 하부 Casing을 기초 라이너 위에 올려놓는데 이때 기초 Bolt는 Casing의 Centering이 완료 될 때까지 완전 조임을 하지 않습니다.
(2) BED와 BEARING HOUSING의 설치
(a) Bearing Housing이 상하 분할인 경우에는 Bed와 하부 Bearing Housing의 분할면에 수준기를 놓고 Level을 조정합니다. 그 다음 Bearing이 조립된 축을 올려놓습니다.
(b) Bearing Housing이 상하 분할 형이 아닌 경우에는 Bed를 소정의 위치에 놓고 Bearing과 Bearing Housing이 모두 조립되어 있는 축을 올려놓아 Bolting합니다. 이때는 양 Bearing간의 축 부분에 수준기를 놓고 Level을 조정합니다.
(NOTE)상기의 Level 조정은 Bed 밑의 기초 라이너를 조정하거나 Bearing Housing 밑에 동판을 끼워 넣음으로써 할 수 있습니다.
3.2.2 양지지형 (Bearing이 Impeller 양쪽에 배치되어있는 경우)
(1) BED설치
Bearing Housing Bed와 Motor Bed를 소정의 위치에 가설치하고 Bed의 높이를 Transit 로써, Bearing간 거리를 줄자로써 측정 조정합니다.
(a) BEARING HOUSING이 상하 분할이 아닌 경우
Bearing Housing Bed위l에 수준기를 놓고 수평도를 가로, 세로, 대각선 방향에 대하여 측정 조정한 후 Bearing Housing Bed의 기초 Bolt를 가볍게 조여 둡니다.
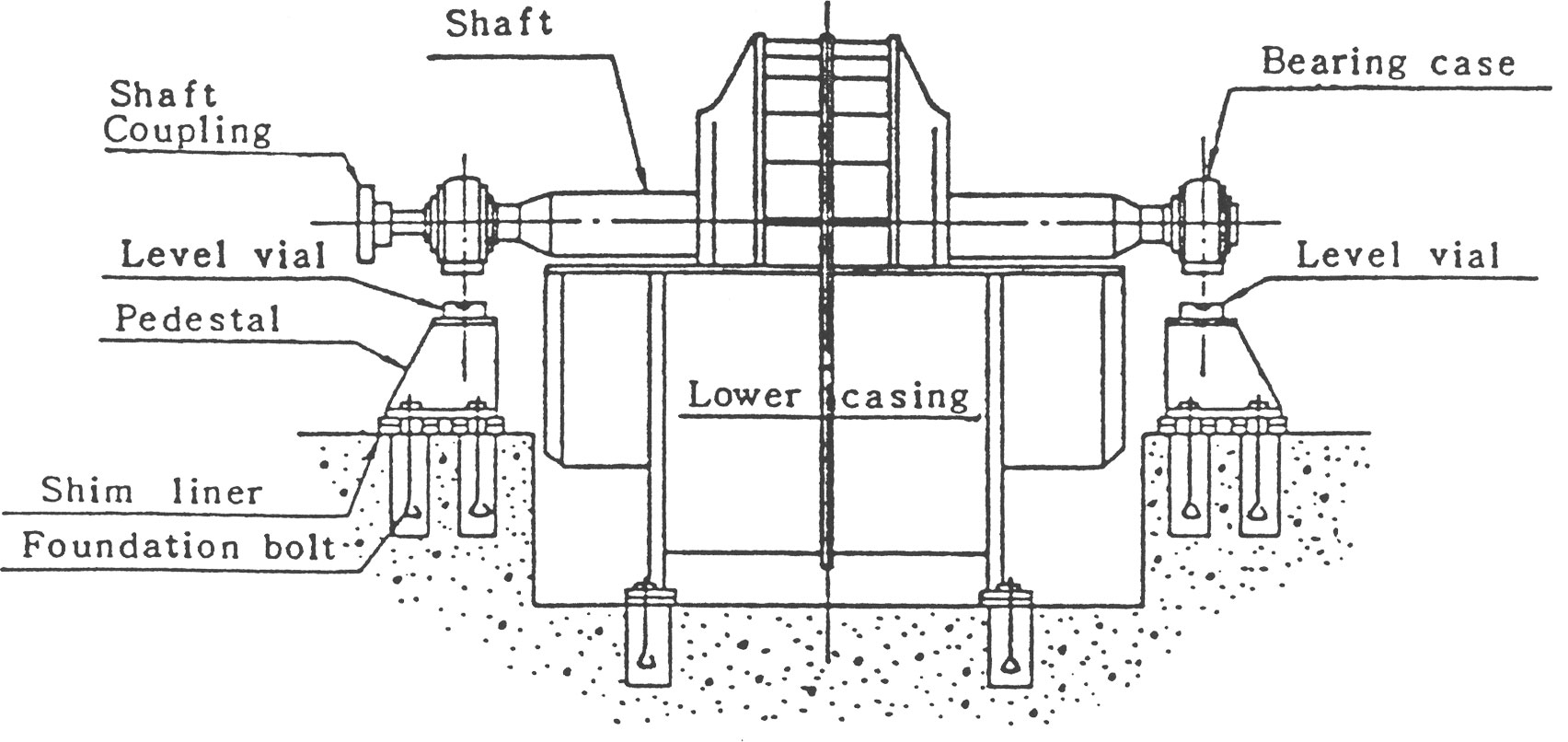
(b) BEARING HOUSING이 상하 분할형인 경우
하부 Bearing Housing을 소정의 위치에 Bolt조임하고, Bearing Housing 분할 면에 수준기를 놓아 전항과 같은 방법으로 Level을 조정한 후 기초 Bolt를 가볍게 조여 줍니다.
(2) 하부 CASING의 설치
하부 Casing을 기초 라이너위에 설치하고 기초 Bolt는 Centering이 완료 될 때까지 완전 조임을 하지 않습니다.
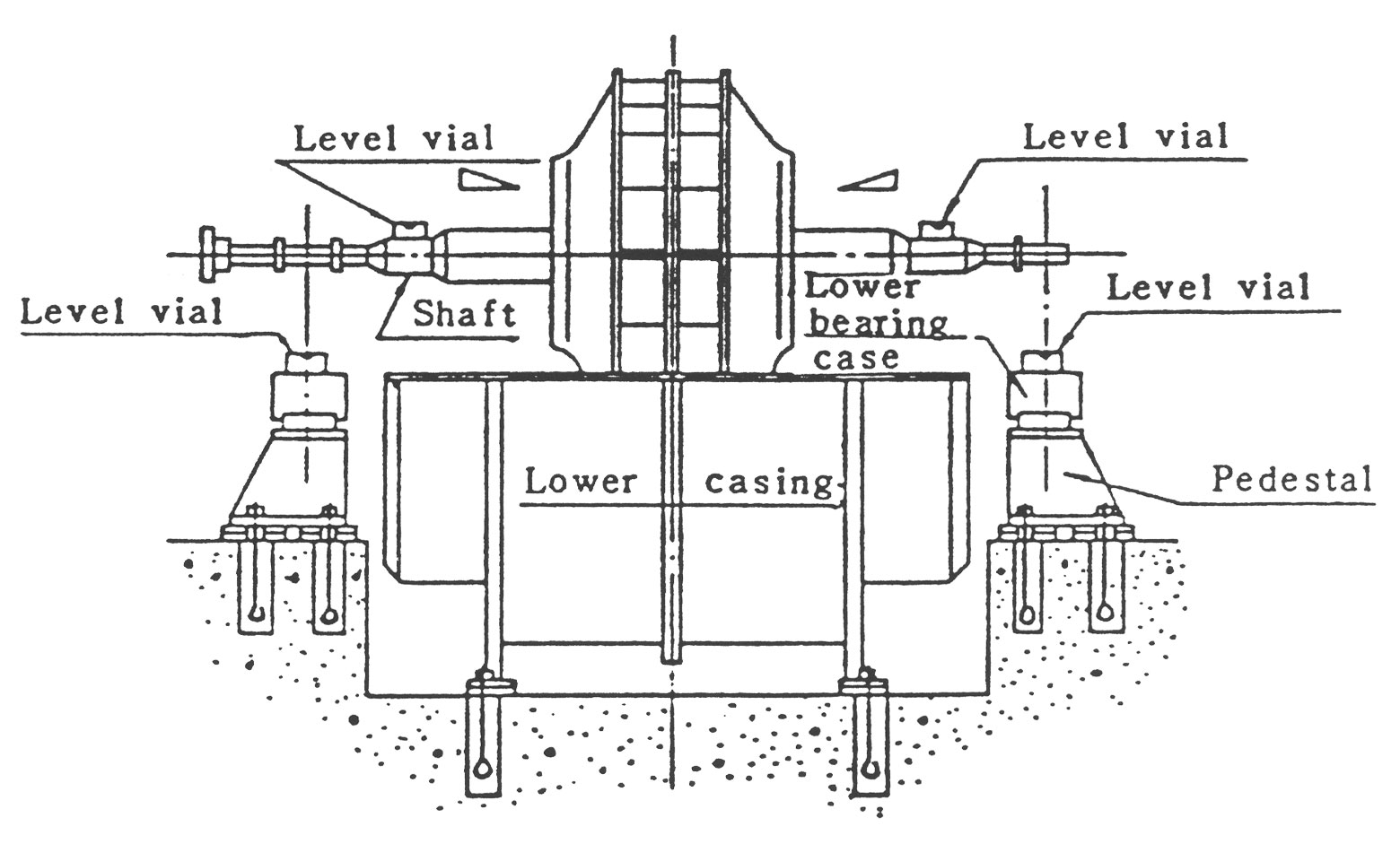
Casing이 Bearing, Motor와 함께 공통 Bed위에 이미 조립되어 납품된 경우에는 우선 전체적으로 Bed를 소정의 위치에 설치하고,, 전하의 (a), (b)와 같은 방법으로 Level을 조정한 후 Bed에 하부 Casing을 붙입니다.
(3) 축의 설치와 조정
Impeller가 조립되어 있는 축을 그림2 혹은 그림3의 방법으로 셋팅한 후 Motor측과 반 Motor측 축 각각의 수평부분에 수준기를 올려놓고 Bed 밑의 라이너를 이용하여 Level을 조정합니다. 이때의 기준은 다음과 같습니다.
-수준기의 좌우 구배의 차가 0.05㎜이하
-Bearing축 관통부와 축과의 틈새 차가 0.2㎜이하로 되게 합니다.
3.2.3 고온 송풍기의 설치
이 경우에도 앞에서 설명된 3.2.1, 3.2.2의 방법이 그대로 적용됩니다. 그러나 운전중 Casing Support는 Sole Plate 위에서 미끌어질수있게 설계되어 있습니다. (조립외형도참조)
(3) Casing은 그림4의 예에서와 같이 하나의 기준점에서 방사상으로 열팽창을 받습니다. 따라서 Casing Support에는 열팽창 기준이 되는 원형구멍이 하나있고 나머지에는 장방형 구멍이 뚫려 있어서 열팽창을 받을 수 있도록 되어 있습니다.
(4) Sole Plate와 Casing Support를 체결해주는 셋팅 Bolt의 위치는 그림4의 우측 그림과 같이 한쪽으로 치우쳐서 배치되어야 합니다.
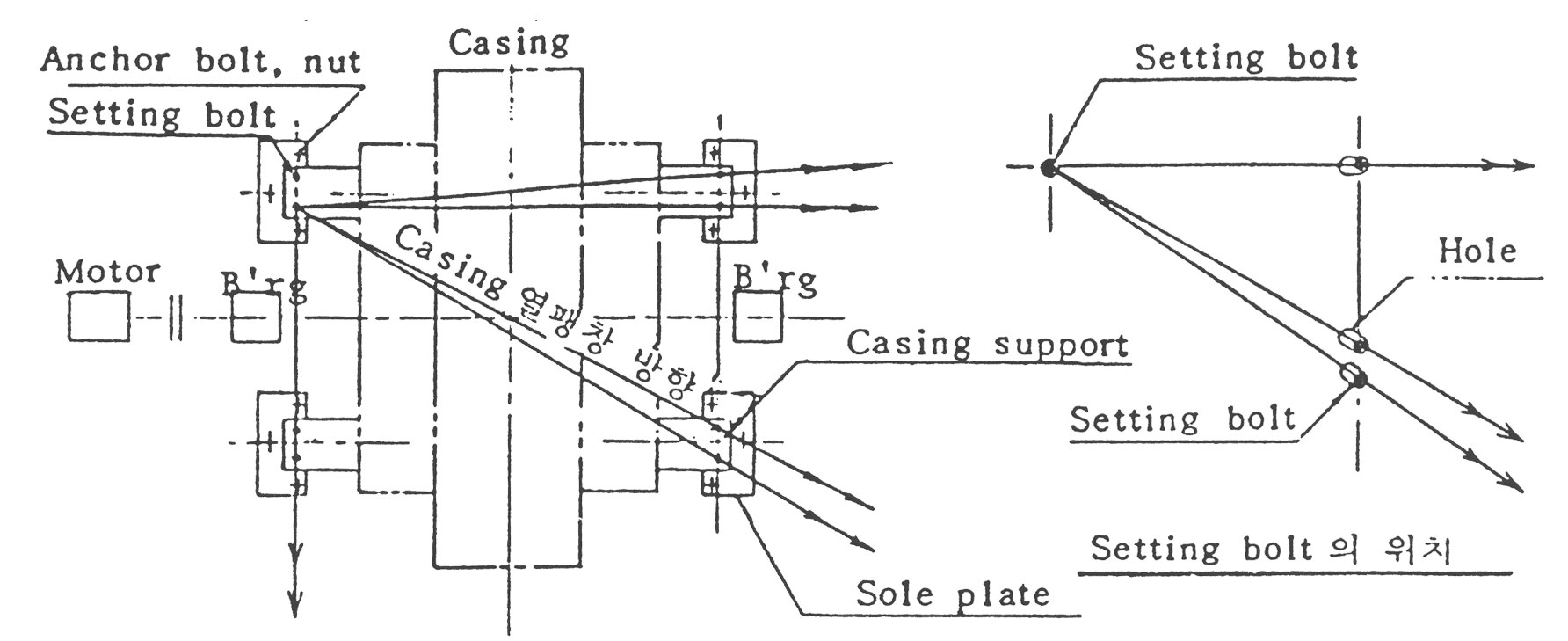
3.2.4 BEARING의 조정 및 BEARING HOUSING의 위치 설정
(1) Bearing Housing이 분할형이 아닌 경우에는 Bearing Cover를, 분할형인 경우에는 상부 Bearing Housing을 떼어 낸 후 Bearing의 눕음을 확인 조정하여 주십시오.
이때 눕음의 허용치는 0.05㎜입니다.
(2) 축의 신장여유를 고려한 BEARING HOUSING의 위치 설정
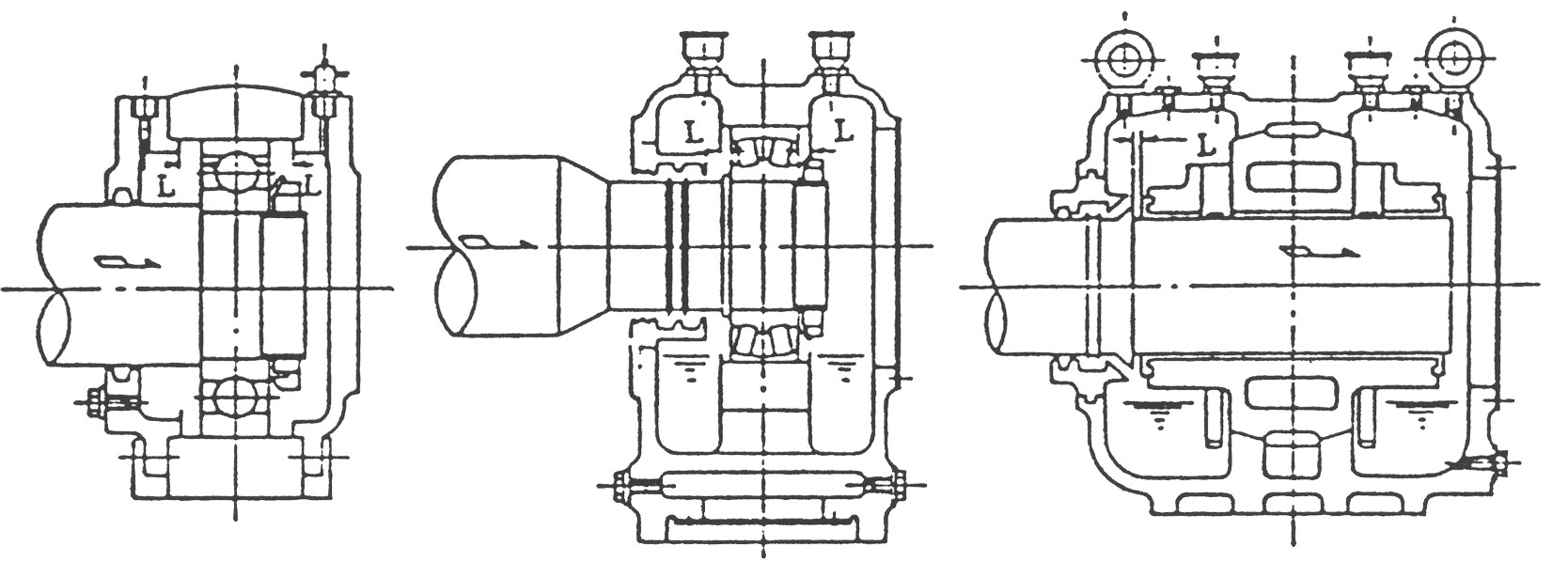
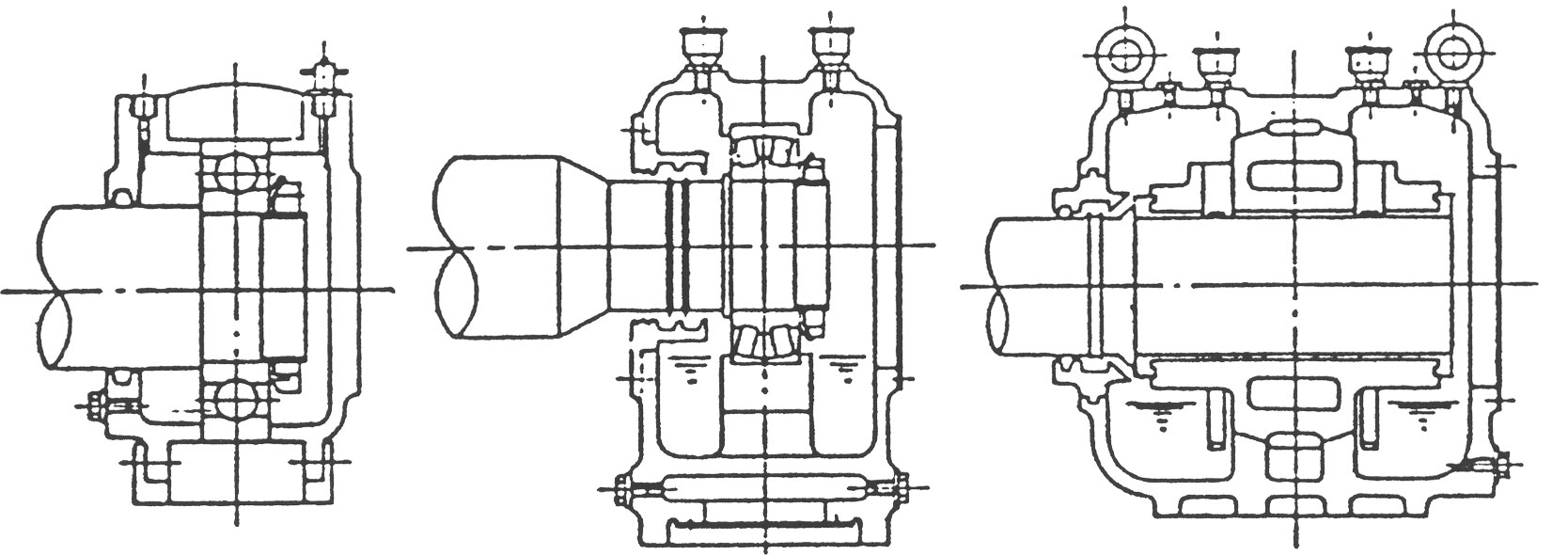
송풍기축은 운전중의 압축열이나 가스온도 때문에 축 방향으로 신장하려고 합니다. 이 때문에 하나의 Bearing은 Bearing Housing에 고정되고 다른 하나의 Bearing은 자유롭게 움직일 수 있도록 설계되어 있습니다.
그림 5는 치수L이 축의 신장여유입니다. 구름 Bearing의 경우 그림 5a, 그림 5b에서 보는 바와 같이 L치수는 통상 좌우 동일합니다만. 특별히 단면도상에 그 치수가 명시되어 있을 때는 이를 준수해 주십시오.
구름 Bearing과 Metal Bearing의 상세한 조립 방법은 보수요령을 참조하십시오.
3.2.5 CASING의 조립과 조정
하부 Casing의 설치, Bearing의 조정, 축과 Bearing Housing의 위치 설정이 끝나면 상부 Casing과 흡입구를 붙이게 됩니다.
(1) 그림 6과 같이 Casing 흡입구와 Impeller가 겹쳐있는 경우 상부 Casing을 먼저 설정한 후 흡입구를 붙여야 합니다.
(2) 상부 Casing을 올려놓을 때는 Impeller와 부딪히지 않게 주의해야 하며 상하 Casing의 Bolt 구멍을 확실히 맞추기 위해서는 맞춤봉을 사용하는 것이 좋습니다.
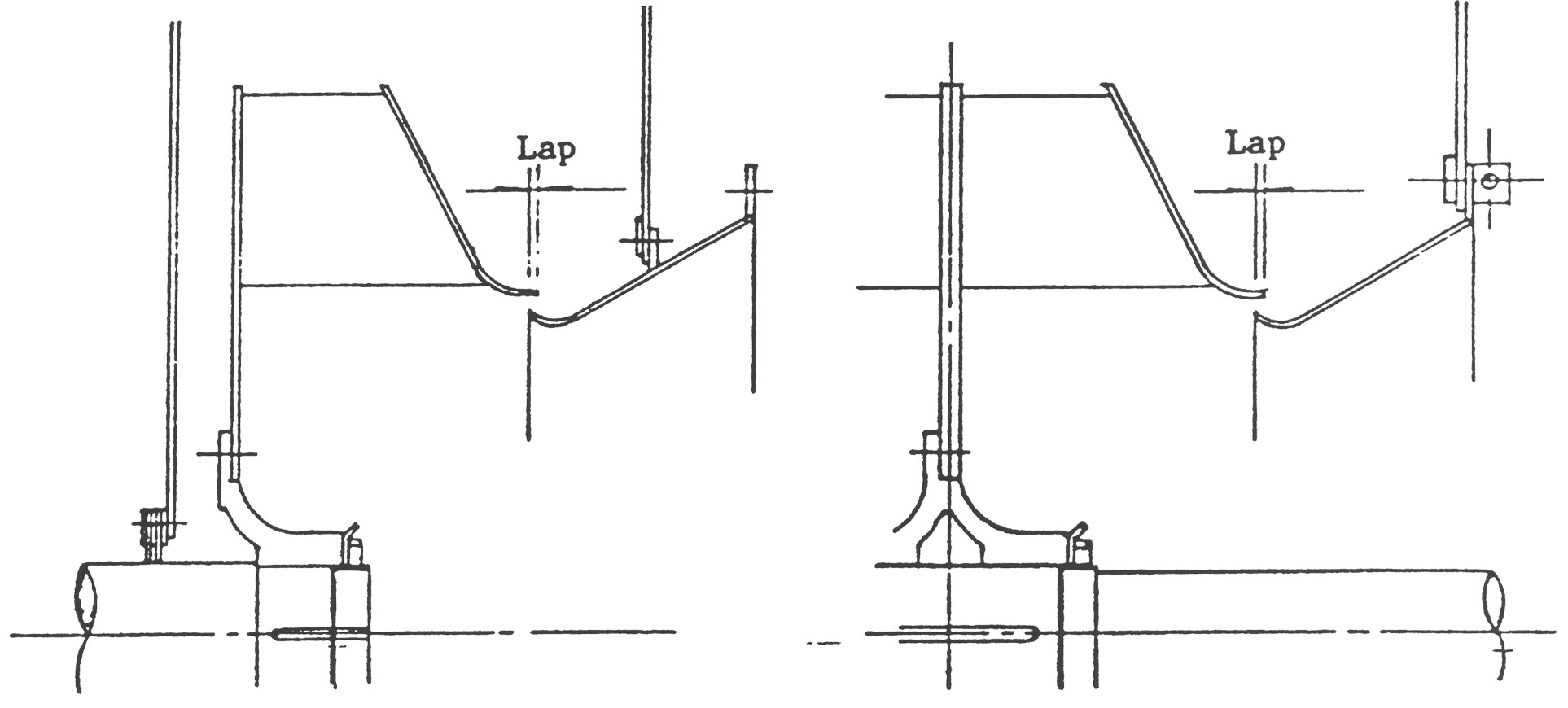
(3) 상부 Casing Damper가 붙어있는 경우에는 Damper Vane을 닫은 상태에서 조립해 주십시오.
(4) 흡입구를 붙인 후에는 Impeller와 축을 기준으로 하여 Impeller와 흡입구와의 틈새, 축과 Casing축 관통부와의 틈새를 각각 90 ̊ 간격으로 측정하고 이들 값이 거의 같게 되도록 조정하여 주십시오.
고온 송풍기의 경우에는 외형도 또는 단면도에 기재되어있는 치수로써 조립해 주십시오.
(5) 축관통부에 그림 7과 같은 Seal Packing을 붙입니다.
고온형 Seal Packing은 Casing의 신장을 흡수할 수 있도록 상하로 미끌어 질수 있는 구조를 갖고 있습니다.
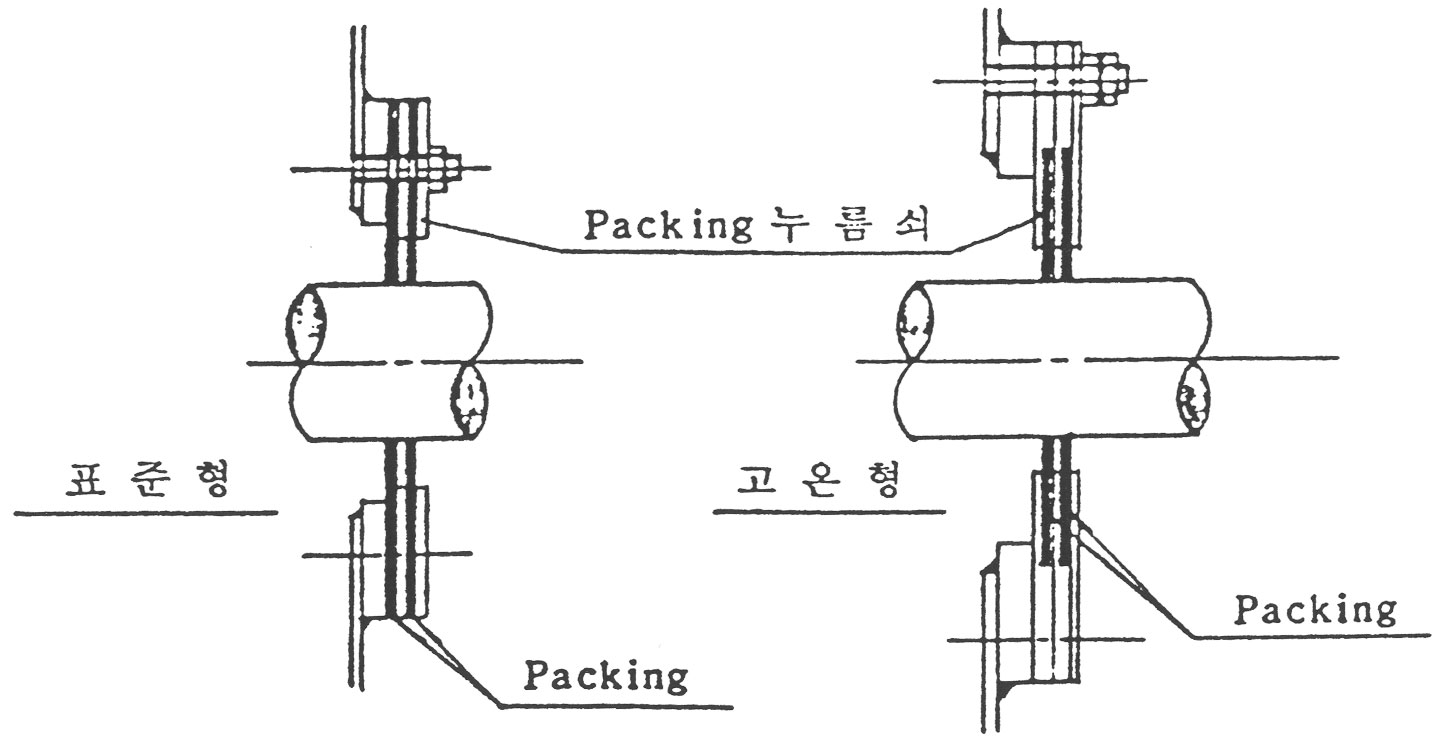
Packing 누름쇠는 축에 닿지 않게 유의해 주십시오.
이것이 축에 닿으면 운전시 사고의 원인이 됩니다.
(6) 상기 조정이 끝나면 모든 Flange에 Bolt를 채우고 기초 Bolt도 채우게 됩니다.
3.2.6 기초 BOLT의 묻음과 재조정
(1) 전체적으로 송풍기의 설치가 완료되면. 각각의 기초 Bolt 구멍에 모르타르를 채우고 이것이 고정된 후 Nut를 조여 둡니다.
(2) Nut 조임 후에 다시 한번 점검하여 설치 치수의 변화, Centering 변화 등을 살피고 필요하면 재조정해 주십시오.
(3) 모든 설치 작업이 끝난 후 Backer Plate와 라이너를 용접하고 기초면 전체에 Mortar Grauting을 실시합니다.
(NOTE) - Centering 작업은 부록1 'Centering 요령 및 기준‘을 참조바랍니다.
- 송풍기의 설치 치수들과 Centering Data는 후일에 중요한 자료가 되므로 반드시 기록 보관하여 주십시오.
3.3 DUCT연결과 CASING INSULATION
(1) Damper가 공급되는 경우 Duct 연결 전에 Damper의 작동상태를 점검하고 Damper Vane의 회전방향을 확인해 주십시오.
(2) Duct 연결시 가능한 송풍기에 Duct의 하중이 걸리지 않도록 해야 합니다. 송풍기에 큰 하중이 걸리면 설치치수의 변동을 수반하는 Casing에 Insulation을 실시할 때는 송풍기의 Insulation시에는 맨홀이나 점검창의 개폐가 쉽게 되도록 유의하여 주시고 Damper의 구동부에는 Insulation을 하지 마십시오.
4.운전
4.1시운전 전 검사
시운전에 들어가기 전 다음 사항을 점검하고 조정해 주십시오.
(1) Casing 내부에 이물질이 없는지 확인합니다.
(2) Impeller를 손으로 돌려서 이상이 없는지 확인합니다.
(3) Bearing Housing과 축, Casing이 축관동부와 축과의 접촉이 없는지 재확인합니다.
(4) 각 Bolt의 조임 상태 특히 Bearing Housing의 Bolt 조임 상태는 Test Hammer로써 두드려서 주의깊게 점검합니다.
(5) Damper의 개폐 조작이 원활한가를 확인하고 Damper Vane을 완전히 닫아 놓습니다.
(6) Bearing에 윤활유가 충진되어 있는지 확인합니다.
(a) 윤활유가 Grease인 경우
당사의 공장 시험때 Grease가 충진되어 그대로 납품되나 재확인이 필요합니다.
(b) 윤활유가 oil인 경우
Bearing Housing에 Grease나 방청유를 도포하여 출하하므로 백등유등으로 깨끗이 씻어낸 후 규정된 oil을 유면계 중앙까지 주유해 주십시오.
(7) Metal Bearing의 경우, 운전 초기에 유막이 끊기는 사례가 있으므로 상부 Bearing Housing의 주유구로부터 손으로 급유하거나 전동기를 저금씩 도려 유막이 형성되게 해주십시오.
(8) Bearing이 수냉식일 경우 냉각수의 흐름을 확인해 주십시오.
(9) Coupling에 Grease가 적절히 주입되어 있는지 충진자에게 재확인합니다.
(10) 운전, 설치등에 관련된 부서와 충분히 상담하여 가동하는 시간을 정하여 둠과 동시에 기동후 이상이 있을 경우의 긴급 정지체제를 확인합니다.
4.2 기동후의 점검
송풍기의 기동과 함께 다음 사항을 점검해 주십시오.
(1) 처음 3분 정도 회전방향을 확인한 후 다시 기동시켜 주십시오.
(2) 이상진동, 이음발생 혹은 Bearing 온도의 급상승이 있는 경우 즉시 송풍기를 정지시키고 예상되는 부품을 재점검해 주십시오.
(3) 이상진동이 생길 때에는 축관통부의 Seal Packing이 축을 강하게 누르고 있는 경우가 많으므로 이 부분부터 점검해 주십시오.
(4) Bearing 온도가 급상승할 때에는 다음 사항을 확인합니다.
(a) 축관통부에 Felt가 쓰이는 경우 이것이 축에 강하게 접촉되어 있지 않는지 그리고 축과 축관통부 사이의 틈새가 균일한지 재확인해 주십시오.
(b) Greaserk 과대 충진되어 있지 않은지 혹은 oil량이 적정한지를 조사해 주십시오.
(c) 상하 분할형이 아닌 Bearing Housing의 경우는 자유측 Bearing Housing의 cover가 Bearing의 외륜을 누르고 있지 않나 재점검 합니다.
(d) 수냉식의 경우 냉각수가 공급되고 있는가 확인합니다.
(e) 구름 Bearing의 경우 Bearing 외륜 및 내륜, Ball 혹은 Poller에 흠집이 없는가를 조사합니다.
(f) Metal Bearing의 경우는 oil Ring의 회전이 정상인가 또 Metal과 축과의 접촉이 없는가를 조사합니다.
oil Ring이 가끔씩 정지하거나 회전이 안되면 oil Ring이 변형되었을 가능성이 있습니다.
(g) Belt 구동이 있을 경우는 Belt의 과대인장 혹은 불균일 인장을 점검해 주십시오.
(5) Bearing의 회전음 조사에는 그림8과 같은 청음봉을 쓰면 편리합니다.
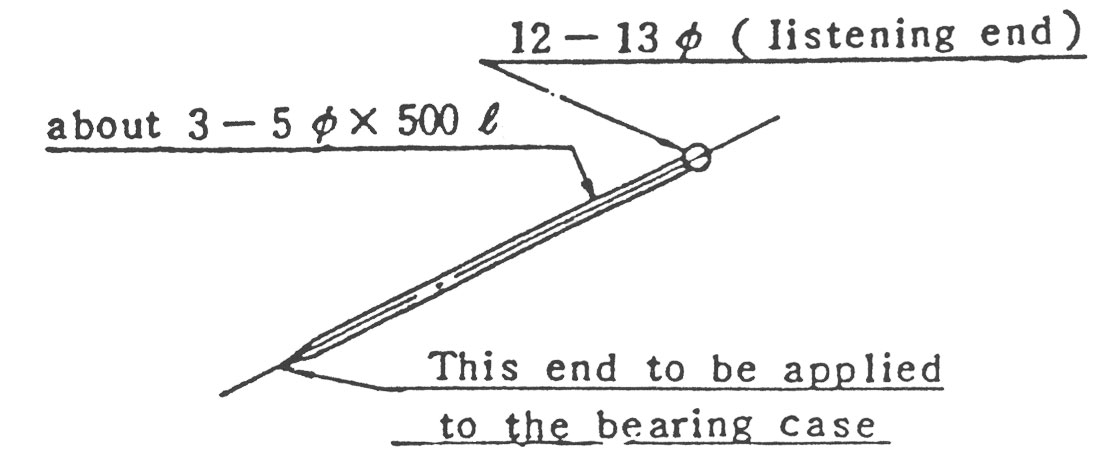
(6) 기동후 이상이 없으면 전류계를 주시하면서 Damper를 서서히 열어주십시오. 고온 송풍기에서는 Gas 온도를 서서히 올려주어 회전 부품등에 온도의 급구배가 생기지 않게 하는 것이 좋습니다.
4.3 운전중의 점검
송풍기의 정상 운전 상태로 들어가면 다음 사항을 정기적으로 점검, 측정 기록해 주십시오. 시운전시에도 점검요령은 같습니다.
(1) Bearing의 온도
Bearing 온도는 주위 온도보다 40℃이상 높아지면 안됩니다만 70℃이하면 지장이 없습니다.
(2) Bearing의 진동
진동은 Bearing Housing에서 3방향 즉 수직, 수평, 축방향을 모두 측정해야 합니다. 첨부1에 진동의 판정기준이 도시되어 있는데 언제나 ‘양호’급 이하로 유지하는 것이 바람직합니다. 진폭 기록시에는 필히 펀진폭인지 전진폭인지 구별해 주십시오.
당사의 시험 성적표에는 전진폭으로 진동치가 기록됩니다.
(3) Bearing이 oil 윤활인 경우 oil의 누유 여부를 확인해 주십시오.
oil이 샐 때는 다음 사항을 점검해야 합니다.
(a) oil이 과도하게 주입되지 않았는가.
(b) Bearing Housing과 Air Vent가 막혀있지 않은가.
(c) Bearing Housing과 축 사이의 기름막이 위치가 정상인가.
(d) Bearing Housing 분할면에 액체 Packing이 도포되어 있는가.
(4) Metal Bearing의 경우 oil Ring의 작동상태가 정상인지 확인해 주십시오.
4.4 정지
송풍기 정지시에는 다음 사항을 지켜주십시오.
(1) Damper를 완전히 닫아 놓읍시다.
(2) Bearing Housing내에서 물이 동결될 우려가 있을 때에는 냉각수를 계속 흘려보내 주내 주거나 Housing 내의 물을 빼 놓습니다.
(3) 고온 송풍기의 경우에는 Casing 내부 온도가 100℃ 정도로 된 후에 정지합니다.
(4) 정지 시간이 길어지면 4~5일에 한번씩 Impeller를 손으로 돌려주거나 전동기로 조금씩 돌려줍니다.
(5) 정지시에 Bearing 윤활유의 열화, 오염도등을 조사해 놓습니다.
5. 보수
5.1 Impeller
(1) Impeller에 부식, 마모, Dust 부착등이 상당히 진행되면 Unbalance와 함께 이상 진동이 발생하므로 정기적으로 Impeller, Casing등을 점검해 주시기 바랍니다.
(2) Dust 부착에 의한 진동은 Dust를 제거함으로써 해결할 수 있습니다만, 부식 마모가 심할 경우에는 Impeller를 수리 혹은 교체해야 합니다.
(3) 현지 Balancing을 실시할 겨우 Balance Weight를 Impeller에 용접하게 되는데, 이때 모재에 Crack이 발생하지 않도록 충분히 주의해야 합니다.
(4) Impeller를 축에서 빼냈을 경우 재조립 순서는 다음과 같습니다.
(a) Impeller Boss 내부를 버너로 가열하여 키와 키홈에 유의하여 Boss를 Flange 끝까지 장입합니다. 이때 Boss와 Flange사이의 틈새가 없도록 해주십시오.
(b) Lock Nut 와 Lock Washer를 끼웁니다.
(c) Boss가 식은후 Lock Nut를 다시한번 조입니다.
(d) Washer의 한끝을 Nut의 홈에 구부려 넣어 완전히 고정시킵니다.
끝 부가 없는 Washer는 Nut의 평평한 부분에 접어놓습니다.
5.2 구름 Bearing
Bearing 교체는 Coupling (혹은 V-Pulley)을 제거한 뒤 다음의 순서로 행해 주십시오.
우선 Bearing 및 조립된 부품을 깨끗이 씻어 둡니다.
Bearing 궤도면과 Ball (혹은 Poller)에 녹이나 흠집이 없는지 확인합니다.
Roller Bearing을 씻을 때는 Roller가 밖으로 빠져나오는 수가 있으므로 주의하여 주십시오.
5.2.1 BEARING HOUSING이 상하 분할형이 아닌 경우
(1) Bearing을 축에 장착하기 전에 그림9b와 같이 내측 Cover에 oil이 충분히 스며들어있는 Felt Ring을 밀어넣고, 이 내측 Cover를 먼저 축에 끼워 놓습니다. 고정측 Cover와 자유측
Cover의 ‘H'치수는 서로 다르므로 주의해 주십시오.
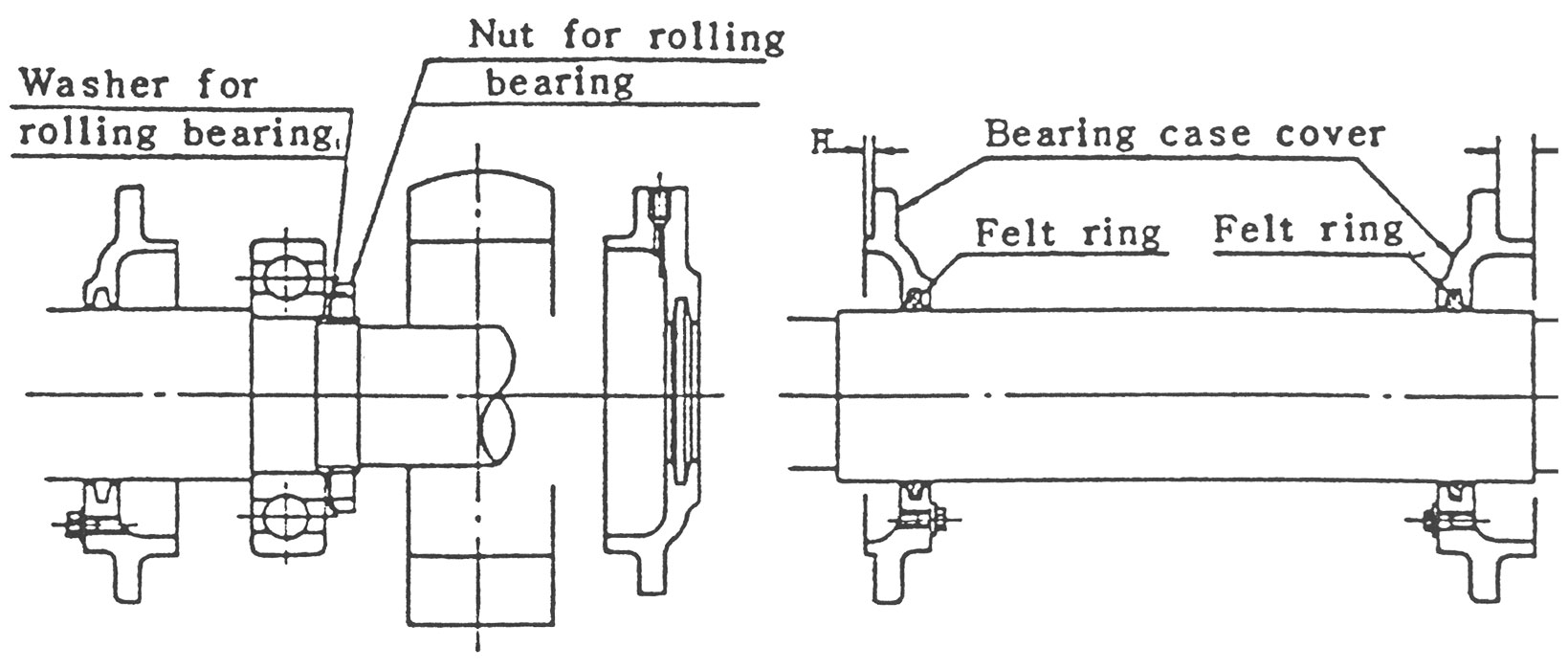
(2) Bearing을 기름통속에서 약 70℃까지 가열한 후 온도가 떨어지기 전에 축에 정착합니다. 이때 Bearing의 내륜, 외륜을 직접 망치로 두드리면 안되며 필요시 Jig를 사용해야 합니다.
(3) Bearing을 축의 Flange 끝까지 축에 직각으로 밀어넣고 틈새가 없도록 밀착시켜 주십시오.
(4) Lock Washer와 Nut를 넣고 조여 줍니다.
(5) Bearing이 식은 후 Nut를 다시 한번 조입니다.
(6) Washer의 한끝을 Nut의 홈에 구부려 넣어 완전히 고정시킵니다.
(7) Bearing Housing에 충분히 발라줍니다.
(9) 자유측, 고정측이 틀리지 않도록 주의하면서 Felt Ring이 장입된 양측의 Cover를 끼워 넣습니다.
(10) Cover를 다시 떼어서 고정측 Cover는 Bearing을 눌러주고 있고 자유측 Cover는 Bearing과 닿지 않는다는 것을 확인해 주십시오.
(11) 양측 Cover를 붙인 후 축관통부와 추과의 틈새차가 0.2㎜이내가 되도록 조정합니다.
(12) 조정이 끝나면 축에 조립된 Bearing Housing을 Bed위에 설치하고 다시 Cover를 제거한 후 그림10의 요령으로 다이알 게이지로써 Bearing의 눕음을 측정 조정합니다.
이때 눈금의 허용치는 0.05㎜입니다.
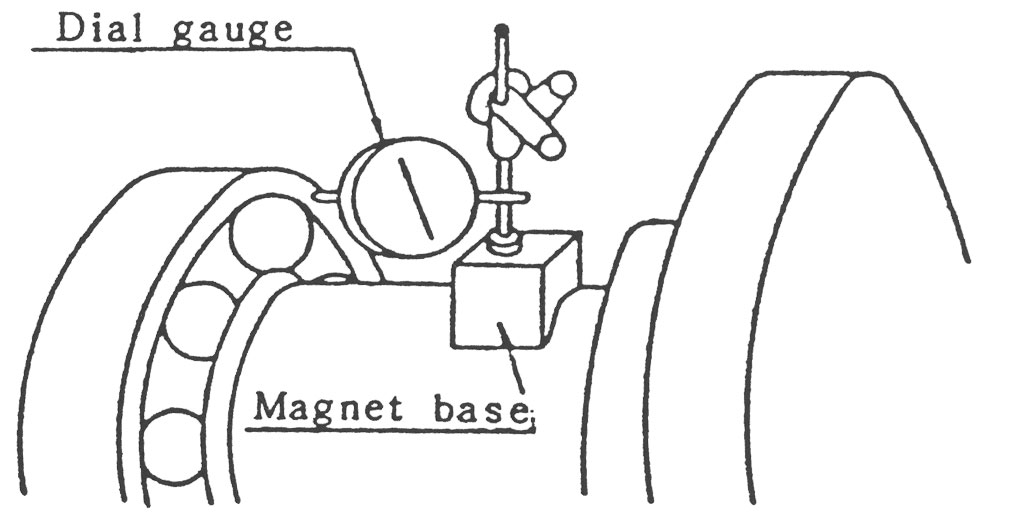
5.2.2 BEARING HOUSING이 상하 분할인 경우
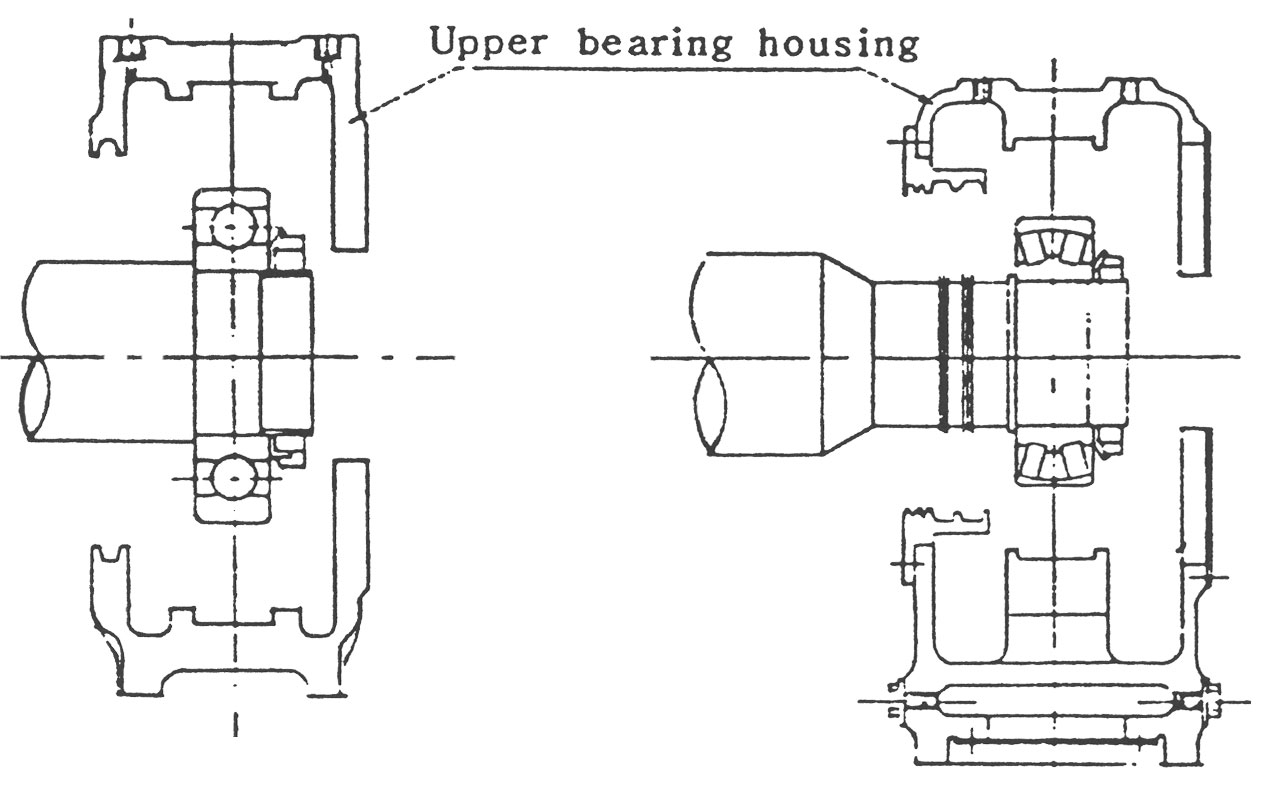
(1) Bearing을 기름통속에서 가열하여 Lock Washer, Nut로 채우는 과정은 5.2.1의 (2)~(6)항과 동일합니다.
(2) oil 윤활인 경우 기름막이를 축의 소정의 위치에 끼워 넣습니다.
(3) Bearing이 조립된 축을, 미리 Bed 위에 설치되어 있는 하부 Bearing Housing에 조립합니다.
(4) 그림10의 요령으로 Bearing의 눕음을 0.05㎜ 이내로 조정합니다.
(5) 분할면에 액체 Packing을 도포하여 상부 Bearing Housing을 붙인 후 축과 축관통부와의 틈새차가 0.2㎜이내가 되도록 조정합니다.
5.3 METAL BEARING
5.3.1 분해
(1) Bearing 냉각용 배관을 제거합니다.
(2) 상부 Bearing Housing을 제거한 후 상부 Bearing Metal을 떼어냅니다. 이때 고정측은 Metal 양측이 축의 Flange와 접촉하고 있으므로 Flange면이 상하지 않게 조심해 주십시오.
(3)Oil Ring을 양옆으로 옮겨 놓읍시다.
(4) 축을 조금 뜨게하여 그림12와 같이 목편을 놓고 망치로 두드려 하부 Bearing Metal을 축에 연하여 돌려 뺍니다.
5.3.2 틈새점검
그림13에서 보듯이 연선을 넣어서 상하 Bearing을 조이고 다음 공식에 의해 축과 Bearing의 틈새를 측정 기록합니다.
틈새 = c-(a+b)/2 (a,b,c : 조임후 측정된 연선의 두께)
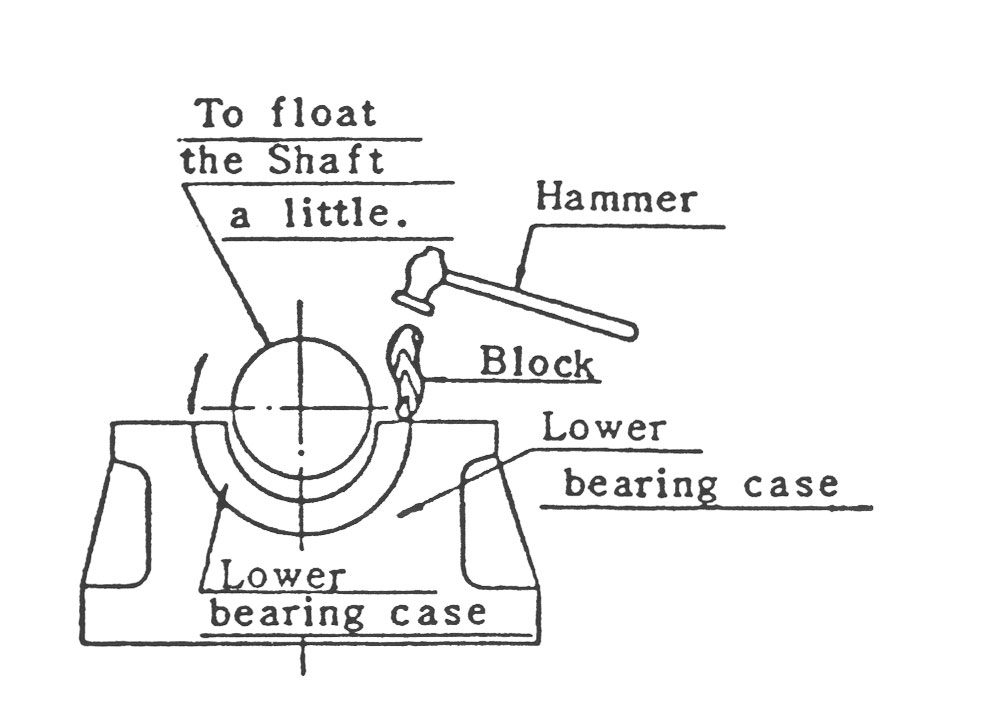
Bearing의 틈새는 조립 단면도에 명시되어 있는데, 측정된 틈새가 이것의 2배 이상이면 Bearing을 교체해야 됩니다.
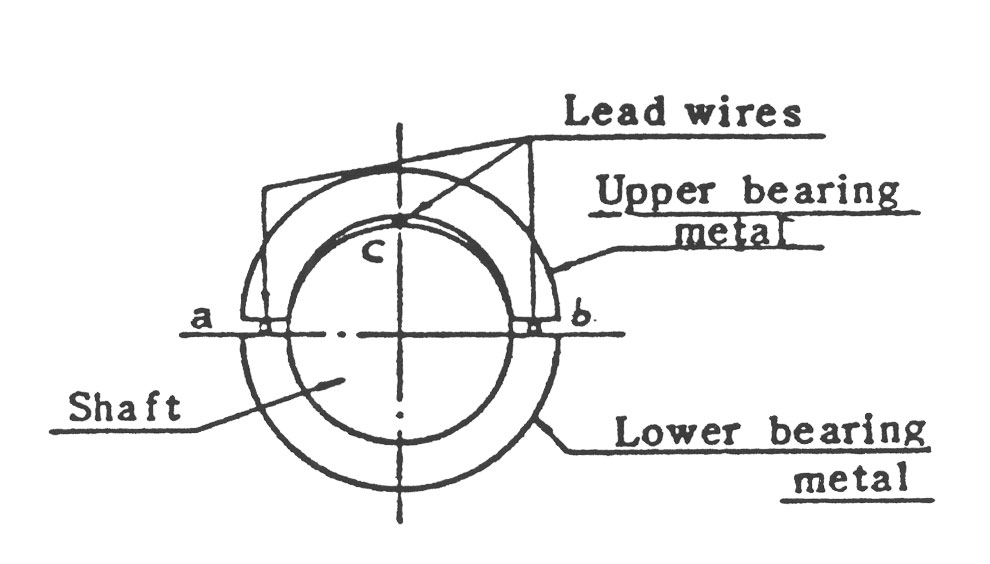
5.3.3 조립
(1) 하부 Bearing Housing을 설치하고 내부를 깨끗이 하고 하부 Bearing Metal을 넣습니다.
(2) 축을 올려놓고 Oil을 소정의 위치에 설정합니다.
(3) 고정측에 특히 주의하면서 상부 Bearing Metal을 조립합니다. 이 과정에서 Oil Ring이 Metal 밑에 끼인 다던지 충격을 받으면 Oil Ring이 변형되므로 주의해야 합니다.
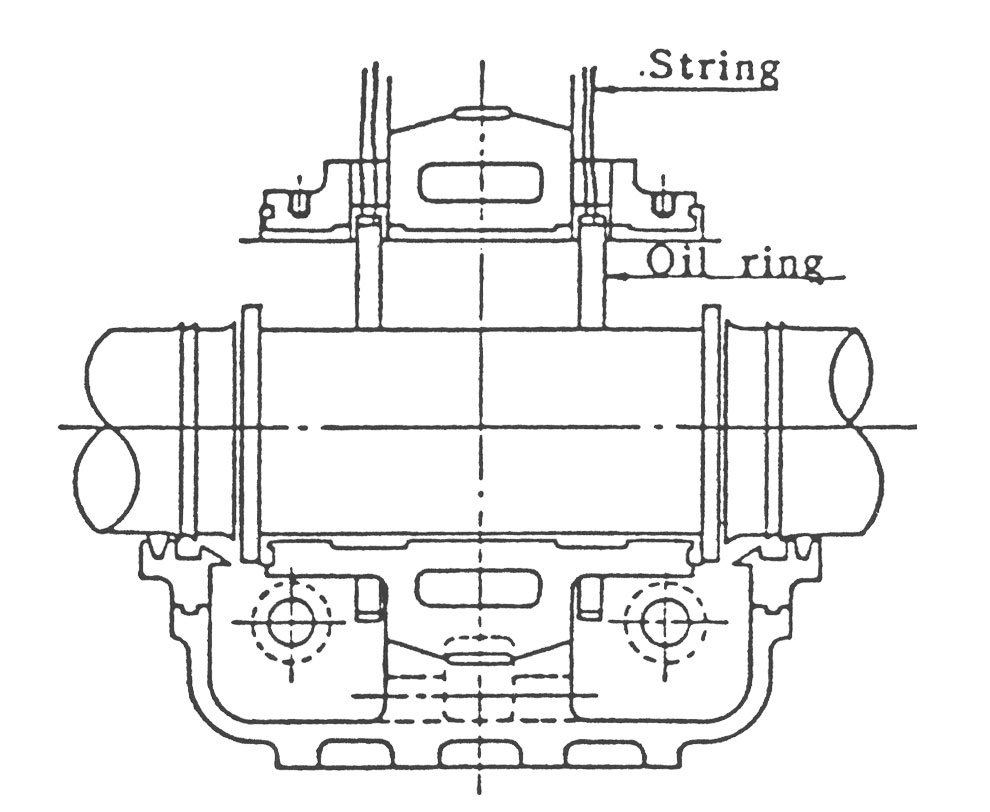
(4) 변형된 Oil Ring을 그대로 사용하면 운전중 Oil Ring이 Bearing에 부딪히거나, 회전이 불량해지거나, 정지됨으로써 사고의 원인이 됩니다. 변형의 허용치 (최대경과 최소경의 차)는 약 3㎜인데 변형량이 3㎜이상일 때는 두드려서 고치지 말고 신제품과 교환해야 합니다.
(5) 그림 14와 같이 Oil Ring을 끈으로 달아매고 상부 Bearing Metal과 함께 내리면 안전하게 조립할 수 있습니다.
(6) 냉각수 배관을 붙입니다.
(7) Bearing Housing 분할면에 액체 Packing을 도포하고 상부 Bearing을 붙입니다. 단 Bearing Metal 분할 면에는 액체 Packing을 도포하지 마십시오. 축과 Bearing Metal 사이에 액체 Packing이 유입되면 Bearing이 손상됩니다.
5.4 전동장치
구동축인 Motor축과 종동축인 송풍기축 사이에 연결되는 동력전달 장치로서는 Steel Flexible Coupling (Grid Coupling), Gear Coupling, Flange Coupling, Diaphragm형 무급유 Coupling, 유체 Coupling, V-belt 등이 사용되고 있으나 어떤 경우이든 별도의 Catalog 혹은 설명서가 첨부되어 있으므로 이를 참조 바랍니다.
5.5 윤활유
5.5.1 Oil
(1) Oil은 가능한 운전 개시후 3개월째 전량 교체하여 주시고 그 후는 1년에 1회 교체합니다. 교체주기 사이에도 정기적으로 Sample을 채취하여 기름의 열화, 산화 등을 검사하는 것이 좋습니다.
(2) Oil의 보충은 상부 Bearing Housing의 Air Vent를 풀어낸 후 이 구멍으로 주유하며 배유시에는 하부 Bearing Housing의 기름빼기 Plug를 빼내면 됩니다.
(3) 사용 Oil의 종류 및 량은 별도의 윤활유 List를 참조하십시오.
5.5.2 GREASE
(1) 통상 1년에 1회 Bearing Housing Cover를 떼고 전량 교체합니다.
(2) 중간에 Grease의 보충이 필요 할 때에는 별도의 윤활유 List를 참조 하십시오. 표1에서 Grease 보충시기 및 보충 주입량이 결정됩니다.
(3) Grease를 지나치게 많이 넣으면 운전중 교반열로 인하여 온도가 비정상적으로 상승되므로 주의해야 합니다.
통상 Grease 주입량은 Bearing Housing용적의 1/2 정도이며 2/3이상 채우면 안됩니다.
5.6 DAMPER
(1) Damper용 Bearing에는 급유가 필요 없습니다.
구름 Bearing (Flange Unit)을 사용하는 경우에도 무급유로 설계되어 있습니다.
(2) Vane Control Damper의 경우에 변형이 없는 한 재조정이 필요 없으나 Vane의 개폐 동작이 원활치 못하거나 정기점검이 필요한 때에는 그림 15의 요령으로 분해 조정할 수 있습니다.
(3) Vane Control Damper의 Control Ring에는 정기적으로 Grease를 주입하여 원활한 작동을 유지시켜 줍니다.
(NOTE) Damper Vane은 언제나 Impeller 회전 방향으로 열리게 되어 있으므로 분해후 재 조립시에는 반드시 이를 기억해 두어야 합니다.
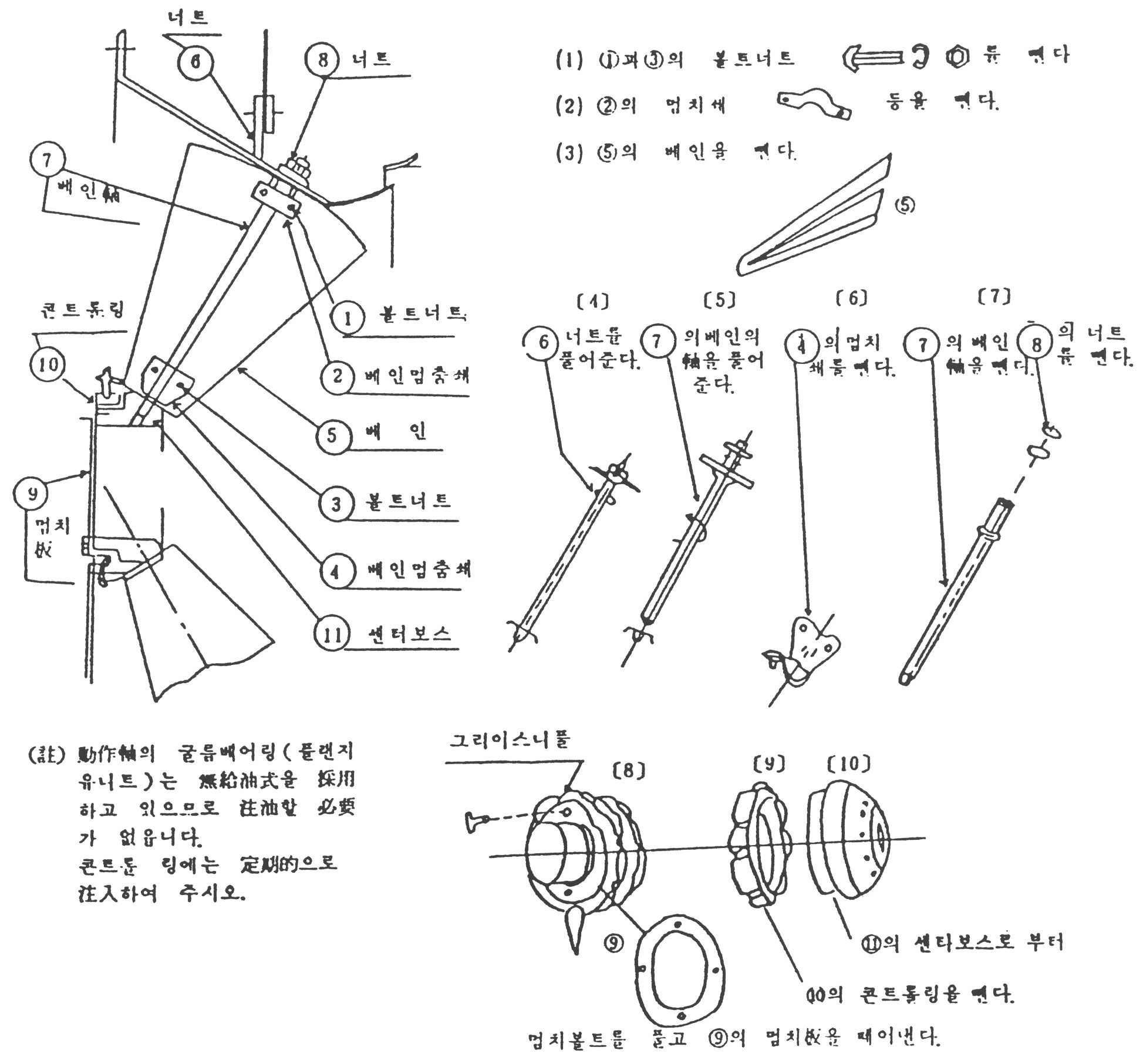
부록. CENTERING 요령 및 기준
1. COUPLING에서의 CENTERING
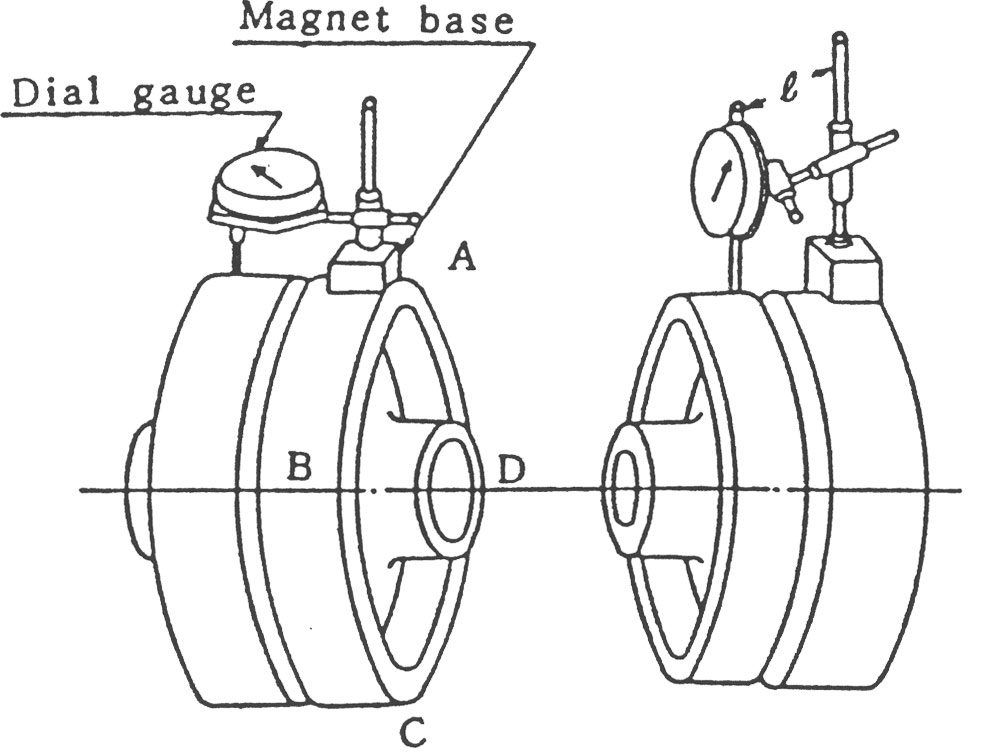
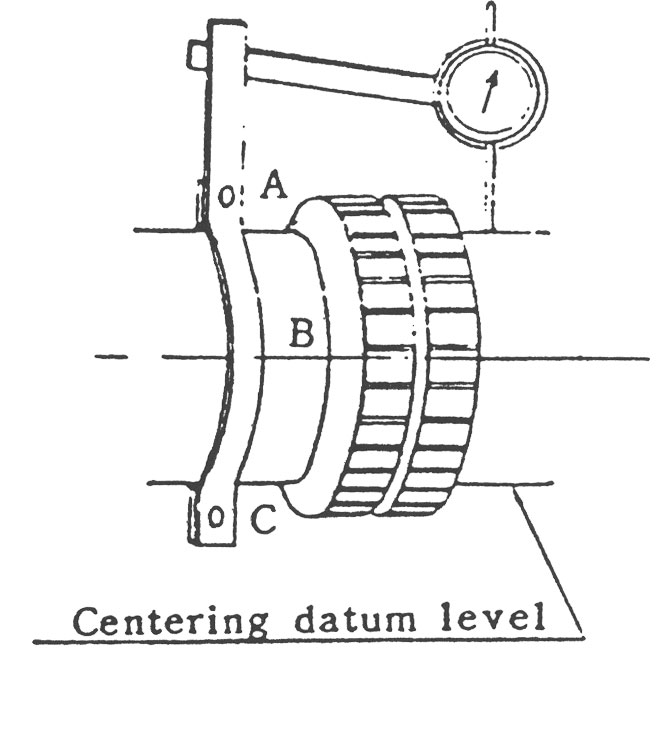
(1) Flange Coupling은 그림1과 같이 Coupling 외주에 다이얼 게이지를 붙여서 Centering 정도를 측정 조정합니다.
Grid Coupling이나 Gear Coupling의 경우에는 Coupling의 심내 기면에 다이얼 게이지를 설정하여 측정하는데 기준면이 좁으므로 붙임쇠를 준비합니다. (그림2)
(2) 다이얼 게이지는 아래쪽으로 돌았을 때에는 지침에 다소의 오차가 발생하는 수가 있으므로 미리 다이얼 게이지를 상하 좌우에 위치 시켰을 때의 지침의 변화를 알아두고 측정치를 수정해야 합니다.
특히 그림1의 우측과 같은 방법에서는 오차가 크게 나타납니다. 또 지점에서 게이지까지의 Arm의 길이는 짧을수록 좋고, 너무 길면 휘어서 오차가 발생합니다.
(3) Coupling 면간의 치수는 Taper Gauge 혹은 두께 Gauge로써 외형도에 표시된 설치 치수로 맞춥니다.
(4) 그림 1,2와 같이 양측 기준면에 90도 간격으로 A, B, C, D의 맞춤 마크를 표시합니다.
(5) 양측의 기준면을 동시에 회전시켜 (즉 Motor 축과 송풍기축을 동시에 회전시켜) A, B, C, D 4점에서의 축심의 불일치 및 두면간의 틈새를 기록 수정합니다.
(6) 양측 기준면의 동시 회전이 곤란한 경우에는 다음 순서로 Error를 수정합니다.
(a) 먼저 송풍기측에 다이얼 게이지를 붙이고 A 점에서의 다이얼 게이지의 눈금을 ‘0’에 맞춘 다음 motor축은 정지 시킨 채로 송풍기만 90도 간격으로 회전시켜 4점의 눈금을 기록합니다.
(b) 다음에는 다이얼 게이지를 옮기후 Motor 축만 회전시키면서 전항과 같은 요령으로 측정합니다.
(c) a, b 항에서 측정한 값의 산술 평균이 Centering 수치가 됩니다.
2. CENTERING의 공차 허용 기준은 다음과 같습니다.
송풍기의 회전수 | 편심 수치 | 두면간의 틈새공차 |
1800 r. p. m. 이하 | 0.05㎜ 이하 | 0.1㎜ 이내 |
1800 r. p. m. 초과 | 0.025㎜ 이하 | 0.05㎜ 이내 |
3.CENTERING에 관한 주의사항
(1) 측정은 2~3회 실시하고 조정은 Motor 밑의 라이너로써 행해 주십시오.
(2) Motor와 Bearing이 공통 Bed 위에 설치되어 납품 되었더라도 반드시 Centering을 재확인 해야 합니다.
(3) Coupling을 연결하기 전에 Motor를 단독 운전하여 회전방향 및 이상 유무를 확인해 주십시오.
(4) Motor는 부하 운전시 온도 상승이 생겨 중심 높이가 다소 높아지므로 C-entering시 이것을 고려하여 Motor 축심을 약간 낮게 설치하는 것이 좋습니다. 그 수치는 대략 Motor 중심높이 ×(1/10000)입니다.
4. V-BELT 와 V-PULLEY의 조정
V-Belt 구동인 경우에는 다음과 같이 조정합니다.
(1) 두개의 V-Pulley 측면에 실 띄우기 등을 하여 V-Pulley의 평행도를 면밀히 점검합니다.
(2) 평행도 조정은 Slide Base 위에 있는 Motor 본체를 움직이거나 Slide Base 밑의 라이너로써 행해 주십시오.
(3) 그림 3과 같이 송풍기축과 Motor축이 서로 평행이 못되거나 삐뚤어진 상태로 설치되면 V-Belt 및 Bearing의 마모가 촉진되며 진동이 발생합니다.
(4) Belt가 너무 과하게 당겨지지 않도록 또 Whirling (Belt가 춤추는 현상)이 없도록 주의하여 주십시오.
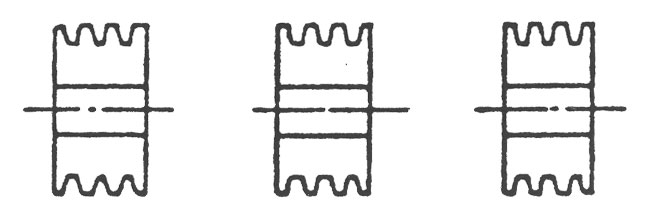
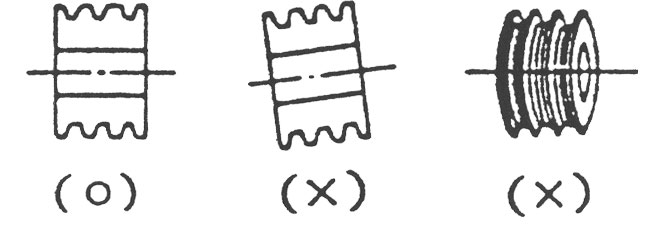
SUS 316L | SUS 304 | SUS310S | ||
화학성분 | C(탄소) | 0.03 이하 | 0.08 이하 | 25 |
Si(규소) | 1 이하 | 1 이하 | ||
Mn(망간) | 2 이하 | 2 이하 | ||
P(인) | 0.045 | 0.045 이하 | ||
S(황) | 0.03 | 0.03 | ||
Ni(니켈) | 12~15 | 8~10.5 | 12 | |
Cr(크롬) | 16~18 | 18~20 | 20 | |
Mo(몰리브덴) | 2~3 | - | ||
Fe | 65 이하 | |||
일반적성질 | 단조온도 | 1040~1150℃(finishing: 930℃) | 980~1260℃(finishing온도 930℃이상) | |
풀림온도 | 1010~1120℃(급냉) | 1040~1120℃(수냉) | ||
경화 | 냉동 가공에서만 가능 | |||
산화피막생성온도 | 870℃: 연속사용시 | 1093 ℃ 연속 | ||
790℃: 단속사용시 | 1040 ℃ 단속 | |||
응력제거온도 | 200~400℃ | 200~400℃ | ||
융점 | 1370~1400˚C | 1425℃ | 1400~1453 ℃ | |
기계적성질 | 탄성계수 | 28000000psi | ||
비전기저항(상온 : Micro ohms-cm) | 72 | |||
비열(Btu/lb/℉)32-212℉ | 0.12 | |||
비중 | 7.89 | 7.94 | 7.98 | |
밀도(21℃) | 0.29lb/cu.in(7.9SG) | |||
항복강도(N/mm2) | 175 | 205 | ||
인장강도(N/mm2) | 480 | 520 | ||
내산화성 | good! | 양호 | good | |
내식성 | 양호 | good | ||
내균열성 | bad | |||
특징 | 내공식성과 고온강도에 우수함, 내임계 부식성이 우수 | 내약품성, 내열성이 뛰어남 | 고온에서 사용가능하도록 만들어진 재료 | |
이용도 | 보일러용 파이프, 해양구조물용으로 사용되는 강종 | 처리수조에 사용 | 열처리로내 치구 및 구조물, 침탄용기, 고온로 부품등의 제작 | |
SUS 304
대표적인 오스테나이트계 스테인리스강으로 18-8강으로 불리며, 내약품성, 내열성이 뛰어나기 때문에 처리수조 등에 사용된다. SUS 304는 Ni 8~11%, Cr 18~20%( 보통 Cr이 Ni의 2배) Fe 65% 이하를 함유한 강이다.
Ni와 Cr의 두가지 원소가 합금되, 부동태 피막이라는 보호층이 형성되 부식을 방지해주는 역할을 한다.
1. 화학성분
C : 0.08%이하 Mn : 2.00%이하 Si : 1.00%이하 P : 0.040%이하
Cr : 18.00 / 20.00% Ni : 8.0 / 10.50%
2. 일반적 성질
A : 단조온도 : 1040 ℃ ~ 1150 ℃( Finishing : 930도)
B : 풀림온도 : 1010 ℃ ~ 1120℃(급냉)
C : 경화 : 냉간가공에서만 가능
D : 산화피막생성온도
870도 : 연속사용시
790도 : 단속사용시
E : 응력제거온도 : 200도 ~ 400도
F : 융점 : 1425도
3. 기계적성질
A : 탄성계수 ; 28000000psi
B : 비전기저항(상온 : Micro ohms-cm)--------------------72.0
C : 비열(Btu/lb/℉)32-212℉ -----------------------------0.12
D : 비중-----------------------------------------------7.94
E : 밀도(21℃ 에서)---------0.29lb/cu.in(7.9SG)
F : 피로강도 (수인상태에서) --------21℃ : 28kg/ ㎟)이하 중복단위 생략
427 : 22.4
538 : 22.4
649 : 21.0
G : 인장강도 : 박판 대(Strip)59.77(kg/㎟)
봉.냉간인발(고장력)77.36~87.90(kg/㎟)
*주의 : 인장강도는 온도에따라 변합니다.
H : 항복강도 : 박판 대(Strip)21-24.5(kg/㎟)
봉.냉간인발(고장력)52.5-66.5(kg/㎟)
I : 연신율(%) : 박판 대(Strip)50-60
SUS 316L
주로 보일러용 파이프, 해양구조물용으로 사용되는 강종이며 316강 특성인 내공식성과 고온강도에 우수한 특성에 내입계부식 특성을 추가하는 강종이다. 내공식성은 금속에 홈모양의 부식이 발생되는 것을 말하고, 구멍의 크기가 작고 부식 속도가 느릴 뿐 아니라 금속표면의 때와 기타의 생성물로 눈으로의 확인이 어려움이 있는 부식이지만 , Pit가 형성되면 빠른 속도로 구멍이 날 때 까지 진행되는 부식으로 316L강은 pitting 부식을 방지하려고, 내식성 및 내열성 향상원소인 Mo(몰리브덴)의 첨가하며, 입계부식을 억제하고 탄소(C)를 0.03%이하를 유지한다.
스테인리스에는 부동태피막이 스테인리스강의 부식을 방지하는데 스테인레스강의 표면에 얇은 산화막이 형성되므로, 대기중에 있는 산소와 산화물과의 접촉을 막아, 산화나 부식, 녹의 발생을 억제하며, 이와 같은 상태를 부동태라고 하고 이와 같은 부동태피막은 금속에 있는 Cr이, O와 반응해 만들어지는 Cr2O3가 Base Metal에 아주 강한 밀착된 피막형태로 나타나지만 그 층의 두께가 워낙 얇은 1~3 X 1/1,000,000,000mm로 육안식별은 불가능하다. 하지만 grain boundry 즉, 철강 조직의 결정입자 경계선에, 금속성분들이 친화력이 강한 금속 원소끼리 집중하는 특성이 있고, 이런 특성에 특성에 따라 경계에 있던 금속성분들이 친화력이 강한 금속 원소끼리 집중하는 특성이 있고, 이런 특성에 따라 경계에 있던 금속조직 알갱이(grain), Cr원자와 C원자가 너무 친화력이 있어 둘이 결합되어 Cr23C6 이라는 탄화물을 만들어지고, 이는 스테인레스강 내부에 함유된 Cr량을 감소시켜, Cr농도를 떨구고, 이는 부동태피막 형성을 저해해 스테인레스강의 강력한 고유기능 특성인, 내부식성을 상실케 해, 녹발생이 되며 이를 입계부식이라고 한다.
따라서 Cr과 반응하는 C의 함유량을 0.03% 이하로 유지하게 된다.
C 0.03%이하, Si1.0%이하,Mn2.0%이하,Cr16~18%,Ni12~16%, Mo 2.0~3%
용도는 화학공업기계나 펄프공업기구,사진현장기구,식품위생기구등 부식성이 강하거나
내열성이 필요한 부분에 사용되어지고 있는 것으로 알고 있습니다.
참고로 316L에서 L의 의미는 탄소함유량이 낮다
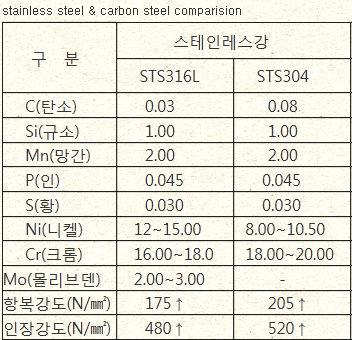
STS310S
310S는
성분은 저탄소25%Cr-20%에서 25%Cr-12%Ni계로 내식성,
내산화성이 좋다.
용착금속은 완전 오스테나이트 조직으로 내균열성은
열악하므로 crater 처리를 한다
1. 단조 온도 : 1260 ℃~980 ℃에서 작업 하며, 마무리 온도는 930℃ 이상 이어야 함
2. 풀림 온도 : 1040 ℃~1120 ℃에서 수냉 처리
3. 산화피막 생성온도 (Scaling Temp, Oxidizing) : 1093 ℃연속(Continuous), 1040 ℃ 단속(Intermittent)
4. 응력제거온도 : 200℃~400℃
5. 융점 : 1400 ℃~1453 ℃
6. 비중 : 7.98
310S 는 고온에서 사용가능하도록 만들어진 재료 입니다.
310S는 열처리로내 치구및 구조물, 침탄 용기, 고온로 부품등의 제작에 사용 됩니다.
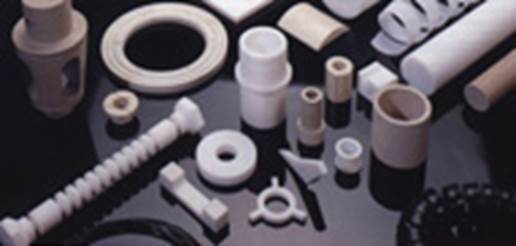
TEFLON (불소계 폴리머)
- PTFE/TFE : Polytetra Fluoroethylene
- PEA : Perflouokoxyfloro Plastic
- FEP : Fluorinated Ethylene Propylene Copolymer
- ETFE : Polyethlene Tetrafluoro Ethylene
- PVDF/PVF : Polyvinylidene Fluoride / Polyvinylfluoride
- PCTFE : Polychlorotrifluoro Ethylene
불소계폴리머란 분자 중에 불소원자를 포함하는 합성고분자의 총칭으로 위에 나열된 제 공중합체가 주를 이루고 있다. 이들 각종 수지는 응용분야에 따라 군수품에서 일반공업용 또는 가정용에도 널리 사용되고 있다.
이들 수지는 뛰어난 내화학약품성과 내열성을 가지고 있으며 양호한 전기절연체로서 높은 충격강도를 가지고 있다.
이중에서도 PVDF는 최고의 유전율, 가열편차온도, 굴곡강도 및 모듈러스를 가지고 있으며 항복강도와 내크리프성은 불소계에서 가장 높다.
이 재료의 내마모성은 PA와 비슷하다. 열 및 광안정성이 대단히 양호하므로 열안정제 또는 자외선안정제를 필요로 하지 않는다. 이것은 이 재료가 무독성이라는 것을 의미하기도 한다.
분자량을 비교적 낮게 유지함으로서 고도의 결정성인 PVDF를 만든다. 이 재료는 제품 강성이 강하므로 성형품용으로 사용되며 불소화폴리머로서는 가공이 비교적 용이하다.
PVDF / PVF
1. 유동성
PP와 비슷하며 멜트는 PA의 멜트보다도 점도가 높다. 225~245℃, 5㎏의 하중에서 1과 18사이에 들어간다.
2. 성형수축
이 재료는 고도의 결정성 수지이므로 수축이 커서 약 2~3%이다. 수축은 금형온도 증가와 함께 조금 증가한다. 수축은 강화그레이드의 사용에 의해 1.5% 즉 0.030㎜/㎜에서 0.020㎜/㎜로 줄일 수가 있다.
3. 강 내성물질
PVDF는 할로겐, 염용액, 무기산과 염기, 지방족과 방향족의 탄소화수소, 카드본산과 산염화물메르캅탄 및 염소화탄화수소 등 광범위한 화학약품에 뛰어난 내성을 가지고 있으며 자외선α 및 β선조사에 의한 열화에 내성이 있다.
4. 약 내성물질
열농유산, 강염기성아민, 열농염기와 알칼리금소그 아세톤 및 에탈아세테이트와 같은 극성 용매에 팽윤한다. 디메틸폼아미드, 디메틸설옥사이드 및 테트라 메틸료소와 같은 용메에 용해한다. 강한 알칼리 속에서는 얼마간의 스트레스 크래킹을 갖는다.
5. 재료의 판정
이 재료의 내추럴컬러는 반투명의 유백색이다. 이 재료는 결정성수지이기 때문에 투명성형품을 만들 수는 없다. 1.78g/㎠의 고밀도를 갖으므로 수중에 용이하게 가라앉는다. 이 수지의 비커트 연화점은 130℃ 정도이다. 결장하는 융점은 170℃ 정도이다. 커트 및 기계가공이 비교적 용이하여 양호항 내인성을 가져서 불꽃을 번지게하지 않는다. 약 320℃에서는 불화수소의 자극성 가스가 발생한다.
6. 착색
이산화티탄이나 무기재료인 산화브롬에서 급속한 분해를 일으킨다. 그러므로 콤파운딩을 할 시는 사전에 재료메이커와 협피磯? 유리충전재는 급속한 분해를 일으키는지 여부를 확인하다. 그러므로 PVDF는 재료메이커로 부터 콤파운딩된 재료를 그대로 사용한다. 또 재료메이커에서 지정한 미스터배치나 드라이컬러만을 사용한다.
7. 용도
화학 프로세스용 밸브, 펌프 베어링 등에 이 재료가 사용된다. 이것은 뛰어난 내화학약품성, 가공의 상대적인 용이성, 높은 강도, 강성 및 내마모성 등이 있다. 높은 결정 융점을 가지고 있어 130℃의 높은 온도에서 연속사용에 견디며 내화학성도 많이 유지한다.
트랜스듀서, 마이크로폰, 라우드스피커 등의 뒤판 부착에 유용된다. 또한 바킹, 가스켓, 파이플, 이음 등 기계부품, 다이서프렘용기 실험기구, 필름, 시트, 프린터기판, 절연단자, 서켓 컨덴서 필름, 고층건축물의 창틀 실링재, 판, 금속판 라이닝, 초음파현미경, 계속센서, 압력센서 등 다양하게 이용된다.
PEA
1. 성질
이 수지는 PTFE의 주고리를 가지고 측고리에 OR기(R은P-클로로알킬기)를 부가한 것이다. 이 수지는 PTFE수지와 물성이 대단히 비슷하다. 용해점이 낮고 용해 시켜서 사출성형이 가능하다.
1) 기계적특성, 전기특성, 열특성 등이 TFE와 비슷하다.
2) 고온 저온 특성이 뛰어나 연속사용온도 260℃에서 -100℃까지 물성변화는 극히 작고 액체공기온도 -196℃에서 사용에 견딘다.
3) 난연성 UL94, V-0, UL83 수직화 염테스트에 합격
4) 방사선의 영향을 받아 3~10메가라드에서 영향을 받아 50메가라드에서 현저하게 열화한다.
5) 전기절연성은 뛰어나고 특히 고주파절연성이 높다. 그리고 PTFE나 FEP와 유사하다.
6) 넓은 주파수 내역에 걸쳐 유전율, 유전정접의 수치가 낮다.
7) PEA필름, FEP필름에 비해 광투과율은 낮다.
8) 사출성형등 용해성형이 가능하다.
9) 불소계수지의 열분해가스는 유독하므로 취급에 주의를 요한다.
2. 용도
내열, 전기, 전자, 전열부품, 프린트기판, 테이프, 절연테이프, 내약품성 바킹, 라이닝 등이며 블로우성형에 의해 액체용 용기가 만들어진다.
ETFE
1. 성질
ETFE는 용해가공이 되며 사출성형등 능률이 양호한 성형법으로 성형이 된다.
1) 넓은 온도범위에서 물성이 안정하여 -200℃에서 +180℃까지 넓은 온도범위에서 기계특성, 전기특성이 변화하지 않으며 180℃에서 연속사용 운전에 견딘다.
2) 전기절연성 특히 고주파특성이 뛰어나다.
3) 강산, 강알칼리, 유기약품에 거의 침해되지 않는다.
4) 자외선을 투과치 않으며 자외선 열화가 적다.
5) 비점착성이 뛰어나다.
6) 독성이 전혀 없다.
7) 용해가공이 되며 사출성형 등으로 성형품이 만들어진다.
2. 용도
전기절연부품, 절연피복, 라이닝, 절연테이프, 방부식테이프, 필름
PVDF
1. 성질
이 폴리머는 불소수지의 일종으로 기계적 성질이 뛰어나 결정성이 높은 수지를 만든다. 또 유전율이 높고 압전성과 같은 특수성질을 가지고 있다.
1) 불소수지 중에서는 기계적강도가 강하고 특히 내마모성이 높다.
2) 내약품성이 뛰어나고 상온에서 디메틸아민, 아세톤 등을 제외한 거의 모든 약품에 침해되지 않으나 75℃ 이상에서는 아민류, 에스테르류, 에테르류에 침해된다.
3) 자외선, 방사선 열화가 작고 내후성이 뛰어나다.
4) 전기절연성이 뛰어나다.
5) 유기재료로서는 큰 압전특성을 갖는다.
특히 2축연신 필름은 큰 압전특성을 가지고 있으며 PVDF의 필름압전 특성은 다음과 같다.
㉠ 유전율이 무기압전체 보다 작다. 그러나 압전전압강도는 높다.
㉡ 경량으로 유연하기 때문에 충격굴곡에 잘 견딘다.
㉢ 기계 인피던스가적기 때문에 물이나 생체와 매칭하기 쉽다.
㉣ Q가 작기 때문에 주파수 레스폰스가 평탄하다.
㉤ 내전압이 크고 큰 입력에도 파괴하지 않는다.
㉥ 유전율과 비열이 작으며 초전감도가 높다.
㉦ 열확산계수가 낮기 때문에 공간분해 능력이 뛰어나다.
2. 용도
- 성형품: 바킹, 가스켓, 파이프 이음 등 기계부품, 다이어 프레인용기,
실험기 필름, 시트
- 전자.전자기기: 프린트기판, 절연단자, 소켓 켄덴서 필름
- 기타: 고층건물의 창틀 실링재, 판, 금속판 라이닝
- 비에소필름응용: 스피커, 마트로폰, 헤드폰, 카트리치, 초음파마이크,
초음파 현미경, 계측센서, 스트레인게이지, 압력센서
PCTFE
1. 성질
반투명 왁스상으로 PVDF보다 투명성이 양호하다. 비중은 2.1~2.2로 기계적 특성은 PVDF와 비슷하다. 전기적인 특성으로서 전기절연성이 양호하나 고주파 특성은 떨어진다. 사용온도는 -50~180℃까지이고 내약품성은 PVDF에 떨어져 할로겐화 용제에 팽윤한다. 이 수지응 사출성형과 압축성형이 가능하나 고가이다.
2. 용도
내열성 전기부품, 필름, 화학기계배관, 바킹, 라이닝
FEP
1. 성질
이 수지는 PTFE와 비슷한 성질을 가지고 있으나 내열성, 전기특성 등의 제특성은 떨어진다. 이 수지는 성형성이 양호하여 사출성형, 압출성형이 가능하다. 외관상으로는 PTFE와 비슷하나 투명성은 조금 양호하다. 비중은 2.12~2.17이며 기계적 특성은 PTFE와 비슷하다. 내열온도가 240℃로 PTFE보다 낮다. 전기적 특성이 역시 PTFE와 비슷하나 Tan δ의 수치가 조금 높다. 또 고주파대역(100MHZ이상)에 있어서 tan δ의 수치에 주파수특성을 가지고 있다. 화학특성으로서는 유기 및 무기약품에 견딘다. 성형성은 PTFE보다는 성형성이 양호하고 열가소성을 나타낸다.
2. 용도
전기적 특성 및 기계적 특성이 PTFE와 비슷하므로 성형하기 쉬운 특성을 이용하여 PTFE의 용도에 사용된다.
대표적 물성치 비교
구 분 | PTFE | FEP | ETFE | PVDF | PCTFE |
비중 | 2.15 | 2.16 | 1.74 | 1.76 | 2.1 |
인장강 | 280 | 200 | 200 | 550 | 350 |
인장신 | 300 | 250 | 400 | 250 | 150 |
굴곡탄 | 4,000 | 3,500 | 6,000 | 10,000 | 15,000 |
충격강 | 16 | 16 | 18 | 15 | |
경도 (노치,㎏.㎝/㎝) |
18 | 25 | 50 | 110 | 90 |
연속사용온도 | < 260℃ | < 200℃ | < 180℃ | < 150℃ | < 180℃ |
흡수율 | < 0.01 | < 0.01 | < 0.01 | < 0.03 | < 0.03 |
융점 | 327℃ | 290℃ | 260℃ | 180℃ | 215℃ |
연소성 | 불연 | 불연 | 불연 | 자기소화 | 불연 |
마모계 | 0.09 | 0.2 | 0.2 | 0.21 | 0.18 |
모터의 종류
1. DC Motor
DC 모터는 모터로서 최초에 발명된 것이다. 원리적으로는 자기장 속의 도체에 전류를 흐르게 함으로써 발생하는 전자기력의 응용인데 이 메커니즘은 플레밍의 왼손 법칙으로 설명할 수 있다. DC 모터는 제어용 모터로서 매우 우수한 특성을 가지고 있다. 예를 들면 급격한 가속성, 큰 시동 토크, 리니어한 회전 특성 등 대체로 제어용 모터에 요구되는 모든 성능을 겸비한 우수한 모터이다. 그러면 여기서 실용적인 DC 모터의 구조에 대하여 설명하기로 한다. DC 모터의 구조는 크게 로터(전기자), 계자용 마그넷, 브러시, 베어링 모터케이스 등으로 이루어져 있다. 브러시의 작용은 전기자에 전류를 공급하기 위한 섭동 접점이다. 또 컴뮤테이터(정류자)는 복수의 전기자 권선에 전류를 공급하는 전류 전환 장치이다. 전기자는 회전력을 발생하기 위한 전자석이고 동시에 모터의 회전체(로터)를 구성하는 것이다. 베어링은 로터의 회전구조를 형성하는 것인데 볼 베어링이나 오일리스 메탈이 사용되고 있다. 계자 마그넷은 전기자 권선에 자력을 주는 것이며 전기자에서 발생하는 전자기력과 함께 회전력을 발생시킨다. 기타 모터 케이스, 앞뒤 커버 등이 있는데 이것은 모터의 회전 구조를 지지함과 동시에 보호 역할을 하는 것이다.
2. 스테핑 Motor
스테핑 모터(Stepping Motor)는 일명 스텝 모터, 펄스 모터, 스테퍼 모터 등이라고 불려지고 있는데 이것을 번역하면 보진 전동기 또는 계동 전동기라고 할 수 있다. 보진은 한 발 한 발 단계적으로 움직이는 것을 말하고 스테핑 모터의 동작 이미지를 잘 표현하고 있다. 그런데 스테핑 모터의 동작 이미지를 잘 표현하고 있다. 그런데 스테핑 모터의 최대 특징은 펄스 전력에 대응하여 회전한다는 것이다. 게다가 입력 펄스수에 비례하여 회전각이 변위되고 또 입력 주파수에 비례하여 회전 속도가 변화하기 때문에 피드백함이 없이 모터의 동작을 제어할 수 있다. 이러한 이점을 가진 스테핑 모터는 피드백계가 없는 위치 결정 제어의 구동원으로 FA, OA 관계를 비롯해서 폭넓게 사용되고 있다. 위치 결정 제어를 다른 모터에서 실현하려면 피드백 제어가 필요하게 된다.
* 스테핑 모터의 개요도
- 특징 및 동작 형태 -
1) 간헐 구동 : 간헐 저속 구동, 1시간에 1스텝, 1일 1스텝 스테핑 모터가 할 수 있는 것 등. 입력 펄스의 주기를 바꾸는 것에 의해 가변 감속(전자적 기어)로 사용할 수 있다.
2) 연속 회전 : 일반 모터와 같은 사용법, 단순한 동력원으로 사용할 수 있다.
회전수는 입력 펄스의 주파수에 비례한다.
총회전수는 입력 펄스의 총수에 비례한다.
3) 정, 역전 : 회전 자기장의 방향을 전환하면 정역전이 된다.
4) 변속 회전 : 입력 펄스의 펄스레이트를 바꾼다(입력 주파수를 가변한다).
5) 다상 구동 : 여자 모드를 전환함으로써 스텝각, 발생토크, 주파수 특성을 변화시킬 수 있다.
6) 마이크로스텝 구동 전기적으로 미세한 스텝각을 실현할 수 있다.
3. 여러가지 스테핑 Motor
스테핑 모터를 분류하는 경우 자기회로, 즉 모터의 구조에 의한 분류법이 일반적이다. 이것에는 로터부를 영구 자석으로 만든 PM형(Permanent Magnet Type), 로터부를 기어 모양의 철심으로 만든 VR형(Variable Reluctance Type), 그리고 로터부를 기어 모양의 철심과 자석으로 구성한 HB형(Hybrid Type)이 있다. PM형은 로터부에 다극착자된 영구 자석을 사용하고 그 둘레에 구동 계자(스테이터)를 설치한 것이다. 이 PM형은 판금 모양의 요크에 발톱을 세운 이른바 크로 폴(craw pole)형이 가장 많이 보급되어 있다. VR형은 로터부에 고투자율 재료를 사용한 기어 모양 회전체를 사용하고 이것과 스테이터 코일에서 발생하는 회전력을 이용한 것이다. HB형은 PM형과 VR형의 장점을 잘 짜맞춘 것인데 스테핑 모터 중에서 가장 우수한 회전 특성르 나타낸다. 또 스테핑 모터의 분류 방법으로는 회전형, 직진형 등의 운동 형태에 의한 분류, 원통형, 박형 등의 겉모양에 의한 분류, 2상, 3상, 5상 등의 구동 권선에 의한 분류, 1상 여자, 2상 뎌자, 1-2상 여자 등의 여자 모드에 의한 분류법도 있다.
4. 브러시리스 Motor
브러시리스 모터(Brushless Motor)는 DC 모터에서 브러시와 정류자(Commutator)를 없애고 전자적인 정류 기구를 설치한 모터이다. 따라서 기계적인 노이즈뿐만 아니라 전기적인 노이즈도 발생되지 않는다. 브러시리스 모터의 장점은 뭐니뭐니해도 원리적으로 노이즈가 발생하지 않는 것이다. 기타 초저속 또는 초고속, 다극(자석의 수가 많다.)긴 수명의 모터가 간단히 만들어지는 점도 장점이라고 할 수 있다. 그런데 브러시리스 모터의 구조는 중심에 회전하는 마그넷이 있고 그 둘레에 구동 코일이 설치되어 있다. 브러시리스 모터의 작동원리는 DC 모터와 같이 플레밍의 왼손 법칙이며 코일 또는 영구 자석의 어느 쪽이 회전해도 그 작동 원리는 같다. 단, 브러시리스 모터에는 정류자가 없기 때문에 이것에 대신하는 전자 정류 회로가 필요하게 된다. 이 회로는 홀 소자 등의 자극 센서를 사용하여 마그넷 로터가 어느 위치에 있는가를 검지하고, 이 신호를 기초로 전자 회로를 제어하여 회전 자기장을 발생시킨다. 이것이 브러시리스 모터의 구동회로인데 매우 회로구성이 복잡하게 되기 때문에 보통은 전용 IC가 사용되고 있다. 브러시리스 모터의 주요한 용도는 VTR의 실린더, 카세트 덱의 캡스턴, FDD, CD 플레이어 등이며 높은 회전 성능, 긴 수명이 요구되는 모터로 사용되고 있다. 본래부터 브러시나 정류자를 필요로 하지 않는 AC 모터는 브러시리스 모터로 분류되지 않는다.
5. 인덕션 Motor
인덕션 모터(Induction Motor)는 AC 모터의 일종이며 회전 자계형으로 분류되어 있는 모터이다. 이 모터의 작동 원리는 고정자 권선에 흐르는 교번(교류)전류에 의해 발생하는 회전 자기장과 로터부에 발생하는 유도 전류와의 상호작용에 의해 생기는 회전력이다. 이 때문에 인덕션 모터를 유도모터라고 부르는 경우도 있다. 그 내부 구조는 로터부(회전자)는 규소 강판을 적층한 것, 슬롯부는 구리나 알루미늄 등으로 농형으로 권선을 형성한 것이 사용되고 있다. 또 이 종류의 인덕션 모터의 토크 발생부는 로터나 스테이터(고정자)의 권선부가 아니고 그 대 부분이 철심에 집중되어 있다. 그리고 인덕션 모터는 부하(토크)에 대응한 회전수로 회전하는데 이것에는 어느정도의 정속성이 있다. 따라서 그다지 엄밀한 정속성이 요구되지 않는 동력용 모터로서 널리 사용되고 있다. 인덕션 모터에도 여러가지 종류가 있으며 소형의 것으로는 단상 콘덴서 구오형이 가장 많이 보그되어 있다. 특성적으로는 입력 전압이 AC 100V, 200V(50/60Hz), 출력 파워가 수 W 이상, 폴수(자극수)는 2극과 4극이 일반적이다. 또 그 회전수 N[RPM]은 다음 식으로 구할 수 있다. 식 중의 f는 전원 주파수, P는 폴수, S는 미끄럼을 나타낸다(S는 동기 속도[전원 주파수에 의존한다]와 회전 속도의 차를 나타내고 회전 속도는 동기 속도보다 조금 낮게 된다.)
N[RPM] = 120f(1 - s) / p
6. 리버시블 Motor
리버시블(Reversible Motor)는 인덕션 모터의 일종이며 우회전, 좌회전 어느 방향으로도 같은 특성이 얻어지게 되어 있는 모터이다. 원리적으로도 인덕션 모터와 같으나 빈번한 정역전에 견디고 큰 시동 토크를 얻기 위해 일반 인덕션 모터와 같이 주코일, 보조 코일의 관계는 없다. 주요한 용도는 세탁기의 소용돌이 발생용 모터, 가종 자동 기기의 구동원등이다. 리버시블(가역) 모터의 특징을 정리하면 다음과 같다.
1) 빈번한 정역전에 적합하다.
2) 시동 특성이 우수하다.
3) 단시간이면 크기에 비해 큰 출력이 얻어진다.
7. 셰이드형 Motor
셰이드형 모터(Shaded Pole Motor)는 단상 교류 모터의 일종이며 1차 코일과는 별도로 1-2회전의 단락 코일(셰이딩 코일)을 감고 이것에 의해 회전 자기장을 발생시키는 모터이다. 일반적으로 AC 모터를 회전시키기 위해서는 2상 이상의 교류를 필요로 하는데 일반 가정용에는 단상 교류밖에 공급되지 않는다. 그 때문에 AC 모터를 움직이기 위해서는 어떤 대책이 필요하게 된다. 예를 들면 콘덴서를 사용하여 위상이 다른 별도의 전원을 만드는 방법도 있다. 셰이드형 모터에서는 콘덴서 대신에 몇 회전의 단락 코일을 감고 이것에 의해 파이(3.14) / 2 이상 위상이 지연된 교류를 만들어 내고 있다. 즉 보통 공급되고 있는 단상 교류와 셰이딩 코일에 의해 만들어 낸 단상 교류를 조합하여 간단한 2상 교류를 실현하고 있다. 세이드형 모터의 특징은 구조가 간단하고 저가격이라는 점인데 수십 W가 한계이고 출력 효율이 낮다고 하는 결점도 있다. 주요한 용도는 소형의 선풍기나 엄밀한 회전특성(회전 변동, 토크 변동)을 필요로 하지 않느 장치 등이다. 셰이딩 코일은 인덕션 모터나 다음 항에서 설명하는 싱크로너스 모터에도 사용할 수 있으며 현재는 수 W의 인덕션 모터에도 많이 사용되고 있다. 또 셰이드형 모터는 그 외관에 의해 스켈린턴 모터(skeletom Motor)라고도 불려지고 있다.
8. 싱크로너스 Motor
싱크로너스 모터(Synchronous Motor)는 교류 모터의 일종이며 전원 주파수에 동기하여 회전하는 모터이다. 이 모터는 전원 주파수와 동기되었을 때 비로소 안정된 회전 특성이 얻어진다는 특징이 있다. 그 때문에 싱크로너스(동기) 모터라는 명칭으로 불려지고 있다. 이 모터는 로터가 동기 속도로 되지 않으면 토크의 발생 방향이 정해지지 않고 진동 등을 수반하여 정지된다. 또 모터에 최대 토크 이상의 부하를 가하면 동기 속도를 유지할 수 없게 되어 로터가 정지된다. 일반적으로 이 현상을 동기이탈, 또는 탈조라고 부르고 있다. 또 동기 이탈에 대하여는 앞에서 설명한 스테핑 모터에도 같은 현상이 나타난다.
N[RPM] = 120f[Hz] / P
싱크로너스 모터의 회전수 n[RPM] 은 위의 식으로 구할 수 있다. 여기서 f[Hz]는 전원 주파수, P는 폴수(자극수)이다. 예를 들면 2폴의 싱크로너스 모터를 50 Hz로 회전시키는 경우 그 회전수는 위의 계산식에 각각의 수치르 대입하면 120*50/2, 즉 3000회전으로 회전하게 된다. 그리고 이것이 60Hz이면 120*60/2이며 3600회전이 된다. 이와같이 전원 주파수를 안정시키면 모터의 회전수도 안정되기 때문에 시계나 타임 스위치 등에 많이 사용되고 있다. 또 싱크로너스 모터에는 영구 자석형, 히스테리시스형, 인덕터형 등이 있으며 용도에 따라 각각 적합 것이 사용되고 있다.
9. 유니버설 Motor
유니버설 모터(Universal Motor)는 직류나 교류로 회전시킬 수 있는 정류자 모터를 말한다. 유니버설이라는 말은 [여거가지 목적에 사용되는 만능]이라는 뜻이며 이 모터를 직류나 교류로 사용할 수 있기 때문에 이 명칭으로 불려지고 있다. 이 모터의 구조는 앞에서 설명한 직류 직권 모터와 같으며 스테이터 코일과 로터 코일에 동일 전류를 흐르게 하며 회전력을 발생시킨다. 따라서 직류나 교류에서 토크의 발생 방향이 일정하게 되어 항상 일정한 방향으로 회전할 수 있게 된다. 또 유니버설 모터는 입력 단자에 공급하는 전압의 극성을 바꾸어도 회전 방향은 변하지 않는다. 유니버설 모터를 교류 전원으로 사용하는 경우 전원주파수의 2배로 맥동하는데 50/60Hz 정도의 주파수이면 그 맥동은 별로 문제가 되지 않는다. 이 모터의 특징은 시동 토크가 크고 고속 회전이 쉽게 얻어진다는 것이다. 그 때문에 전차 등의 구동 모터로 많이 사용되고 있따. 한편 결점으로는 브러시와 정류자가 있기 때문에 전기 노이즈, 기계 노이즈가 크고 수명도 그다지 길지 않다는 점 등을 들 수 있다.
* 유니버설 모터의 장점과 단점
-장점
1)직류와 교류로 모두 사용할 수 있다.
2)시동(가동) 토크가 크다
3)고속 회전이 쉽게 얻어진다.
4)마그넷을 사용하지 않는다.
5)전압의 극성이 바뀌어도 회전 방향은 일정하다.
-단점
1)무부하 회전수가 높다.
2)전기 노이즈, 기계 노이즈가 크다.
3)수명이 짧다.
10. 리니어 Motor
리니어 모터(Linear Motor)라고 하면 자기 부상식 고속 열차를 연상 할는지 모르나 본래 리니어 모터란 다이렉트로 직선 운동을 하는 모터의 총칭이다. 우리 주변에서 사용되고 있는 모터의 대부분은 회전식인데 각종의 가전제품이나 정보 기기에는 여러 곳에서 직선 운동형 모터가 사용되고 있다. 예를 들면 HDD, FDD의 헤드 이송 장치, 프린터, 재봉틀, 편직기, 자동 도어 컨베이어 등에는 리니어 모터가 사용되고 있다. 그런데 단순히 직선 운동만 시키느 것이면 회전형 모터에 볼나사를 병용하면 된다. 그러나 그 동작의 정밀도, 속도 등의 대한 요구가 높아지면 회전용 모터로는 대응할 수 없게 된다. 그래서 등장한 것이 리니어 모터이다. 이모터는 다이렉트로 직선 운동을 하기 때문에 정밀도와 속도가 상당히 높아진다. 리니어 모터의 종류로는 직류 교류에 한정하지 않고 대체로 어떤 모터로도 리니어 모터로 될 수 있다. 단, 그 성능, 경제성을 고려하면 그 종류도 자연히 한정된다. 예를 들면 직류이면 스테핑 모터나 브러시리스 모터, 교류이면 싱크로너스 모터, 인덕션 모터 등이 사용되고 있다. 리니어 모터의 장점은 앞에서도 설명한 바와 같이 다이렉트인 직선 운동이나 고속 작동이 가능한 것 외에 백래시가 없다. 수명이 길다 등이다. 한편 단점으로는 일반적으로 고가로 되기 쉽다는 것이다.
11. 초음파 Motor
초음파 모터는 자석이나 권선을 필요로 하지 않느 새로운 형의 구동원이다. 작동원리는 복수의 압전 세라믹을 사용하고 이것에 고주파 전압을 가하여 압전 세라믹을 진동시킨다. 그리고 이 진동력에서 탄성체, 마찰판을 거쳐 일정 방향의 구동력, 즉 회전력을 얻는 것이다. 또 그 구동력은 회전형 외에 직진형(린니어 구동형)도 있다. 앞에서 초음파 모터는 새로운 형의 구동원이라고 하였는데, 종래 모터라고 하면 자석이나 권선을 사용하는 전자기의 모터를 지칭하였다. 그런데 이 초음파 모터는 20kHz 이상의 초음파 영역을 사용하는 전기력 모터인 것이다. 초음파 모터의 용도는 저속 회전에서 큰 힘을 필요로 하는 다이렉트 드라이브용 또 자기 에너지를 싫어하는 장치의 구동원, 또는 초소형 사이즈의 구동원, 버니어 구동(미크론 단위의 미소 구동원) 등에 이용되고 있다. 초음파 모터에는 정재파 방식과 진행파 방식이 있으며 일반적으로는 후자의 진행파 방식이 이용되고 있다. 진행파 방식이란 압전 세라믹스를 금속의 탄성체에 맞붙인 스테이터와 로터부를 마주 접촉시켜 탄성체에 발생하는 종파와 횡파에 의한 진행파에서 구동력을 얻는 방법이다. 또 초음파 모터느 그 진동 주파수에 20kHz 이상의 초음파를 사용하고 있으며 이것은 모터 내부에서 그 배부분이 회전력으로 변환되기 때문에 인간이나 기타 생물에게 해르 주는 일이 없다.
12. 슬롯형과 슬롯리스 Motor
모터의 전기자에는 얼마간의 권선을 필요로 하며 철판을 쳠 장 겹친 철심에 슬롯(홈)을 부착하고 여기에 코일을 감아 넣은 형식의 모터르 슬롯형 모터(Slotted type Moter)라고 한다. 이 모터는 구동용 코일을 직접 슬롯 안에 감아 넣기 때문에 보빈은 필요없고 게다가 구조는 매우 단단하게 된다. 그러나 돌극구조이기 때문에 코깅이 발생하고 이것이 토크 변동, 회전 변동 특성에 나쁜 영향을 주게 되는 단점도 있다. 한 편 슬롯이 없는 노터 이른바 슬롯리스 모터(Slotless Motor)는 철심 등에 슬롯이 없고 코일도 본딩 와이어(자기 융착선)를 사용하여 자립 형성하고 있다. 또 슬롯리스 모터는 어떤 위치에 있어도 균일한 자기 흡인력을 받기 때문에 코깅 현상이 없다.
13. 기어드 Motor
기어드 모터(Geared Motor)는 모터의 회전축에 기어 등의 감속 기구를 부착한 것이며 이것에 의해 모터 단체로는 얻을 수 없느 저속 회전이 실현되거나 큰 토크를 발생시킬 수 있다. 또 기어(감속 기구)는 어떤 모터에도 부착할 수 있고 바꿔 말하면 어떤 모터라도 기어드 모터가 될 수 있는 것이다. 그런데 모터는 고속 회전시킬수록 효율이 좋고 경제성도 높아진다. 그 때문에 필요로 하는 회전수의 수십배, 수백배로 모터를 회전시키고 여기에 기어를 짜맞추어 감속하며 최종적으로 목적으로 하는 회전수를 꺼내고 있다(발전기 등은 기어로 증속할 수도 있다).
기어가 부착된 모터의 경우 기어에 의한 감속에 대응하여 그 토크도 증대되므로 비교적 소형의 모터에서도 쉽게 큰 토크를 얻을 수 있다. 기어드 모터의 응용 예로는 카메라에 사용되고 있는 필름 자동 감기 장치, 자동차의 시동 모터, 전동 드라이버, 그 밖에 큰 토크를 필요로 하는 여러가지 장치에 폭넓게 사용되고 있다. 또 기어드 모터의 종류로는 래크와 피니언을 물리게 한 직진 운동(왕복 운동)형, 윔 기어형, 유성 기어형 등이 있다.
14. 스캐너용 Motor
모터의 명칭은 전원의 종류, 구조, 크기, 성능, 사용 목적 등에 의해 여러가지 호칭법이 있느데 여기서 설명하느 스캐너용 모터는 사용 목적에 의한 명칭이다. 정보 기기에서는 스캐너라고 하는 말을 자주 듣게 되는데 이것은 모터의 회전축에 폴리건 미러(다면 거울)를 설치하고 이 거울로 레이저 빔을 선모양으로 달리게 하는 주사장치이다. 스캐너용 모터는 사용 목적에 의한 분류이기 때문에 모터의 구조와 직접적인 관계가 없다. 그러나 그 요구 정밀도가 매우 엄격하기 때문에 모터이면 어떤 것이나 좋다고 할 수 없다. 따라서 스태너용 모터로 사용되는 것은 AC 구동의 싱크로너스 모터(히스테리스 싱크로너스 모터)나 DC 구동의 브러시리스 모터에 한정되어 있다. 어느 것이나 엄격한 지터 특성이 요구되고(0.01% 이하), 또 모터 설치부, 미러 설치부에도 엄밀한 가공 정밀도(수 micro meter)가 요구된다. 이 모터는 스캐너용 이외에 레이저 프린터, 복사기, 팩시밀리 등에도 사용되고 있다.
15. 인코더 부착 Motor
인코더를 간단히 설명하면 여러가지 정보를 보호화 하는 일종의 변환기라고 말할 수 있다. 인코더의 종류에는 그 구조에 따라 리니어식 인코더, 로터리식 인코더가 있으며 각각 리니어 모터, 회전형 모터에 사용되고 있다. 기타 인코더의 기능 분류로서는 인크리멘터리형과 앱솔루트형이 있다. 인크리멘터리형은 회전축의 회전 각도를 출력 펄스의 형으로 변환하는 방식이고 한편 앱솔루트형은 회전축의 위치를 2진 또는 2진화 10진수 등의 부호로 변환하는 방식이다. 또 인크리멘터리형은 회전량의 변화는 검출할 수 있으나 절대적인 위치느 검출할 수 없다. 이 때문에 Z축 신호를 별개로 빼내고 여기에서의 변화를 카운트하여 정확한 위치를 구하도록 연구되어 있다. 이와 같은 인코더가 부착되어 있는 모터를 인코더 부착 모터라고 한다. 인코더의 역할은 회전축에 설치된 슬릿 원판(부호판)의 회전에 의해 A, B, C상의 회전 신호를 빼내고 이들의 신호에서 정확한 위치, 회전량, 속도 제어를 하는 것인데, 인코더 부착 모터는 일종의 서보모터라고 할 수 있다. 또 인코더 부착 모터의 주요한 용도는 공업용 로봇, 공작 기계, 가종 제어 장치 등에 폭넓게 사용되고 있다.
'동력과 에너지 > Motor' 카테고리의 다른 글
모터의 전달함수 구하기 (0) | 2016.10.24 |
---|---|
극수변환모터 (0) | 2016.06.28 |
thermogaurd (0) | 2016.06.28 |
전동기의 보호 방식과 절연 등급 (0) | 2016.06.28 |
전동기의 출력 회전수 (0) | 2016.06.28 |